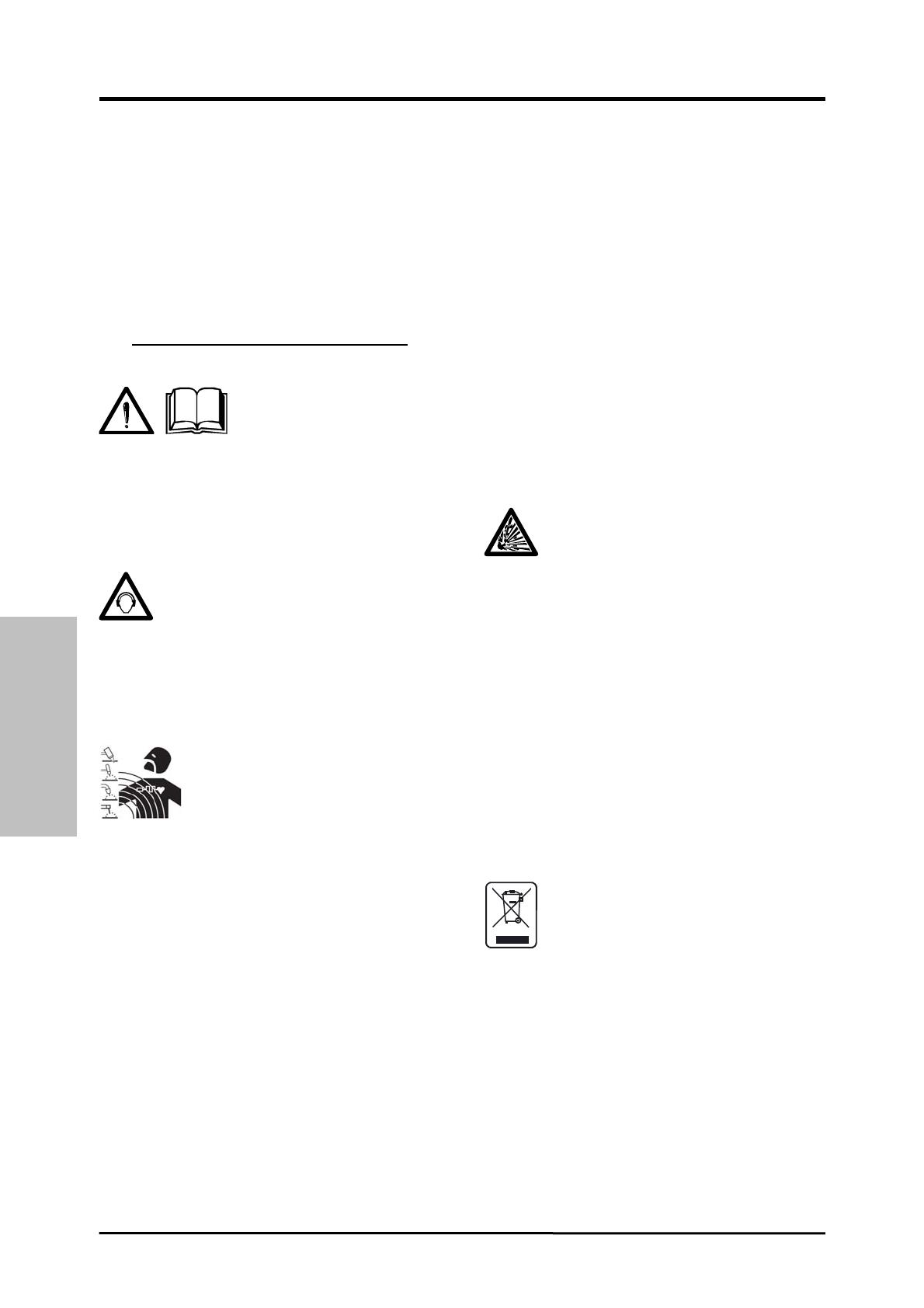
CEBORA S.p.A. 16
3.300.217-A 24-04-2013
E
IMPORTANTE: ANTES DE LA PUESTA EN
FUNCIONAMIENTO DEL APARATO, LEER
EL CONTENIDO DE ESTE MANUAL Y
CONSERVARLO, DURANTE TODA LA
VIDA OPERATIVA, EN UN SITIO
CONOCIDO POR TODOS LOS
INTERESADOS. ESTE APARATO DEBERÁ
SER UTILIZADO EXCLUSIVAMENTE PARA
OPERACIONES DE SOLDADURA.
1 PRECAUCIONES DE SEGURIDAD.
LA SOLDADURA Y EL CORTE DE ARCO
PUEDEN SER NOCIVOS
PARA USTEDES Y PARA
LOS DEMÁS, por lo que el
utilizador deberá ser informado de los riesgos,
resumidos a contiuaciόn, que derivan de las
operaciones de soldadura. Para informaciones
más detalladas, pedir el manual cód. 3.300.758.
RUIDO.
Este aparato no produce de por sí
ruidos superiores a los 80dB.
eneradores.
El procedimiento de corte
plasma/soldadura puede producir niveles de ruido
superiores a tal límite; por tanto, los utilizadores
deberán actuar las precauciones previstas por la
ley.
CAMPOS ELECTROMAGNÉTICOS.
Pueden ser dañosos.
La corriente eléctrica que atraviesa
cualquier conductor produce
campos electromagnéticos (EMF).
La corriente de soldadura o de
corte genera campos electromagnéticos alrededor
de los cables y g
Los campos magnéticos derivantes de corrientes
elevadas pueden incidir en el funcionamiento de
los pacemaker.
Los portadores de aparados electrónicos vitales
(pacemaker) deben consultar el médico antes de
acercarse a las operaciones de soldadura de arco,
de corte, desagrietamiento o de soldadura por
puntos.
La exposición a los campos electromagnéticos de
la soldadura o del corte podrían tener efectos
desconocidos sobre la salud.
Cada operador, para reducir los riesgos derivados
de la exposición a los campos electromagnéticos,
tiene que atenerse a los siguientes
procedimientos:
- Colocar el cable de masa y de la pinza
portaelectrodo o de la antorcha de manera que
permanezcan flanqueados. Si posible, fijarlos
junto con cinta adhesiva.
- No envolver los cables de masa y de la pinza
portaelectrodo o de la antorcha alrededor del
cuerpo.
- Nunca permanecer entre el cable de masa y el
de la pinza portaelectrodo o de la antorcha. Si
el cable de masa se encuentra a la derecha del
operador también el de la pinza portaelectrodo
o de la antorcha tienen que quedar al mismo
lado.
- Conectar el cable de masa a la pieza en
tratamiento lo más cerca posible a la zona de
soldadura o de corte.
- No trabajar cerca del generador.
EXPLOSIONES.
No soldar en proximidad de recipientes
a presión o en presencia de polvos,
gases o vapores explosivos. Manejar
con cuidado las bombonas y los reguladores de
presión utilizados en operaciones de soldadura.
COMPATIBILIDAD ELECTROMAGNÉTICA.
Este aparato se ha construido de conformidad con
las indicaciones contenidas en la norma
armonizada IEC 60974-10 (CL.A), y se deberá
usar solo de forma profesional en un ambiente
industrial. En efecto, podrían presentarse
potenciales dificultades en el asegurar la
compatibilidad electromagnética en un
ambiente diferente del industrial.
RECOGIDA Y GESTION DE LOS RESIDUOS
DE APARATOS ELÉCTRICOS Y
ELECTRÓNICOS.
No està permitido eliminar los aparatos
eléctricos junto con los residuos solidos
urbanos!
Segun lo establecido por la Directiva
Europea 2002/96/CE sobre residuos de aparatos
eléctricos y electrónicos y su aplicaciόn en el
ámbito de la legislación nacional, los aparatos
eléctricos que han concluido su vida útil deben
ser recogidos por separado y entregados a una
instalación de reciclado ecocompatible. En
calidad de propietario de los aparatos, usted
deberá informarse con nuestro representante local
sobre los sistemas aprobados de recogida.
Aplicando lo establecido por esta Directiva
Europea mejorará la situación ambiental y la
salud humana.