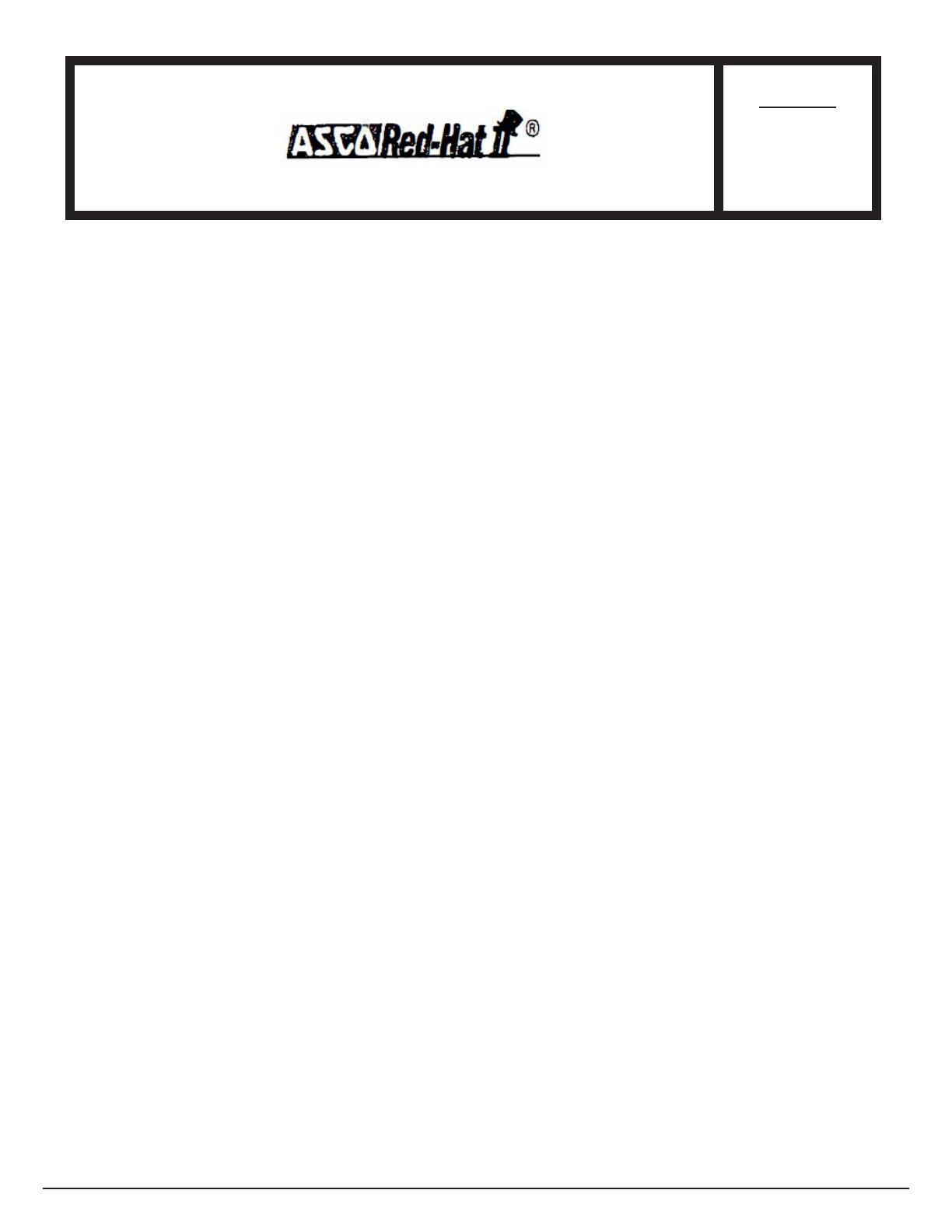
lnstallaon & Maintenance Instrucons SERIES
8003G/H
8007G/H
8202G/H
l&M V 6584 R16 sec1
OPEN-FRAME, GENERAL PURPOSE, WATERTIGHT/EXPLOSIONPROOF SOLENOIDS
ASCO® solenoid valves with design change letter
“G” or “H’’ in the catalog number ( ex. 821 0G I) have
an epoxy encapsulated ASCO® Red Hat II® solenoid.
This solenoid replaces some of the solenoids with
metal enclosures and open frame constructions. Follow
these installation and maintenance instructions if your
valve or operator uses this solenoid.
See separate instructions for basic valve.
* DIN Plug Connector Kit No. K236034: Use this kit
only for solenoids with DIN terminals. The DIN plug
connector kit provides\a two pole with grounding con-
tact DIN Type 43650 construction (See Figure 6).
OPERATION
Series 8003G/H and 8007G/H - When the solenoid is energized,
the core is drawn into the solenoid base sub-assembly.
IMPORTANT: When the solenoid is de-energized, the initial
return force for the core, whether developed by spring,pres-
sure, or weight, must exert a minimum force to overcome re-
sidual magnetism created by the solenoid. Minimum return
force for AC construction is 11 ounces, and 5 ounces for DC
construction.
Series 8202G/H - When the solenoid is energized, the disc
holder assembly seats against the orice. When the solenoid is
de-energized , the disc holder assembly returns. IMPORTANT:
Initial return force for the disc or disc holder assembly,
whether developed by spring, pressure, or weight, must
exert a minimum force to overcome residual magnetism
created by the solenoid. Minimum return force is 1 pound, 5
ounces.
INSTALLATION
Check nameplate for correct catalog number, service, and watt-
age. Check front of solenoid for voltage and frequency.
A WARNING: Electrical hazard from the acces-
sibility of live parts. To prevent the possibility of
death, serious injury or property damage, install
the open • frame solenoid in an enclosure.
FOR BLACK ENCLOSURE TYPES 7 AND 9 ONLY
ACAUTlON: To prevent re or explosion, do not install
solenoid and/or valve where ignition temperature of hazard-
ous atmosphere is less than 165’C. On valves used for steam
service or when a class “H” solenoid is used, do not install
in hazardous atmosphere where ignition temperature is less
than 180’C. See nameplate/ retainer for service.
NOTE: These solenoids have an internal non-resetable thermal
fuse to limit solenoid temperature in the event that extraordinary
conditions occur which could cause excessive temperatures.
These conditions include high input voltage, a jammed core,
excessive ambient temperature or a shorted solenoid, etc. This
unique feature is a standard feature only in solenoids with black
explosionproof/dust-ignitionproof enclosures (Types 7 & 9).
A CAUTION: To protect the solenoid valve or operator,
install a strainer or lter, suitable for the service involved
in the inlet side as close to the valve or operator as possible.
Clean periodically depending on service conditions. See
ASCO Series 8600 and 8601 for strainers.
DESCRIPTION
Catalog numbers 8003G/H, 8007G/H and 8202G/H and are ep-
oxy encapsulated pull-type soleoids. The green solen01d with
lead wires and 1/2 conduit connection is designed to meet En-
closure Type !-General Purpose, Type 2-Dripproof, Types 3 and
3S-Raintight, and Types 4 and 4X-Watertight. The black solenoid
on catalog numbers prexed “EF” or “EV” is designed to meet
Enclosure Types 3 and 3S-Raintight, Types 4 and 4X-Watertight,
Types 6 and 6P-Submersible, Type7, Explosionproof Class I,
Division! Groups A, B, C, & D and Type 9, -Dust-lgnitionproof-
Class II, Division! Groups E, F & G. The Class II, Groups F &
G Dust Locations designation is not applicable for solenoids or
solenoid valves used for steam service or when a class “H” so-
lenoid is used. See Temperature Limitations section for solenoid
identication and nameplate/ retainer for service. When installed
just as a solenoid and not attached to an ASCO valve, the core
has a 0.250-28 UNF-2B tapped hole, 0.38 or 0.63 minimum full
thread.
NOTE: Catalog number prex “EV” denotes stainless steel
construction.
Solenoid catalog numbers 8202G/HI, 8202G/H3, 8202G/ H5 and
8202G/H7 are epoxy encapsulated push-type, reverse-acting so-
lenoids having the same enclosure types as previously stated for
Catalog numbers 8003G/Hl and 8003G/ H2. 8007G/H are 3-way
solenoid operators with a pipe port or adapter, exhaust protector
or vent at the top of the solenoid base sub-assembly.
Series 8003G/H, 8007G/H and 8202G/H solenoids are avail-
able in:
Open-Frame Construction: The green solenoid may be
supplied with 1/4” spade, screw or DIN terminals. (Refer to
Figure 4)
Panel Mounted Construction: These solenoids are speci-
cally designed to be panel mounted by the customer. Refer to
Figures specied in this l&M and the section on Installation
of Panel Mounted Solenoid for details.
Optional Features For Type 1 • General Purpose Construction
OnlyJunction Box: This junction box construction meets Enclosure Types
2, 3, 3S, 4, and 4X. Only solenoids with 1/4” spade or screw terminals
may have a junction box. The junction box provides a 1/2” conduit
connection, grounding and spade or screw terminal connections within
the junction box. (See Figure 5)
- SERVICE NOTICE-
l&M V 6584 R16 sec1
©ASCO Valve, Inc. 50 Hanover Road, Florham Park, New Jersey 07932
www.ascovalve.com
10