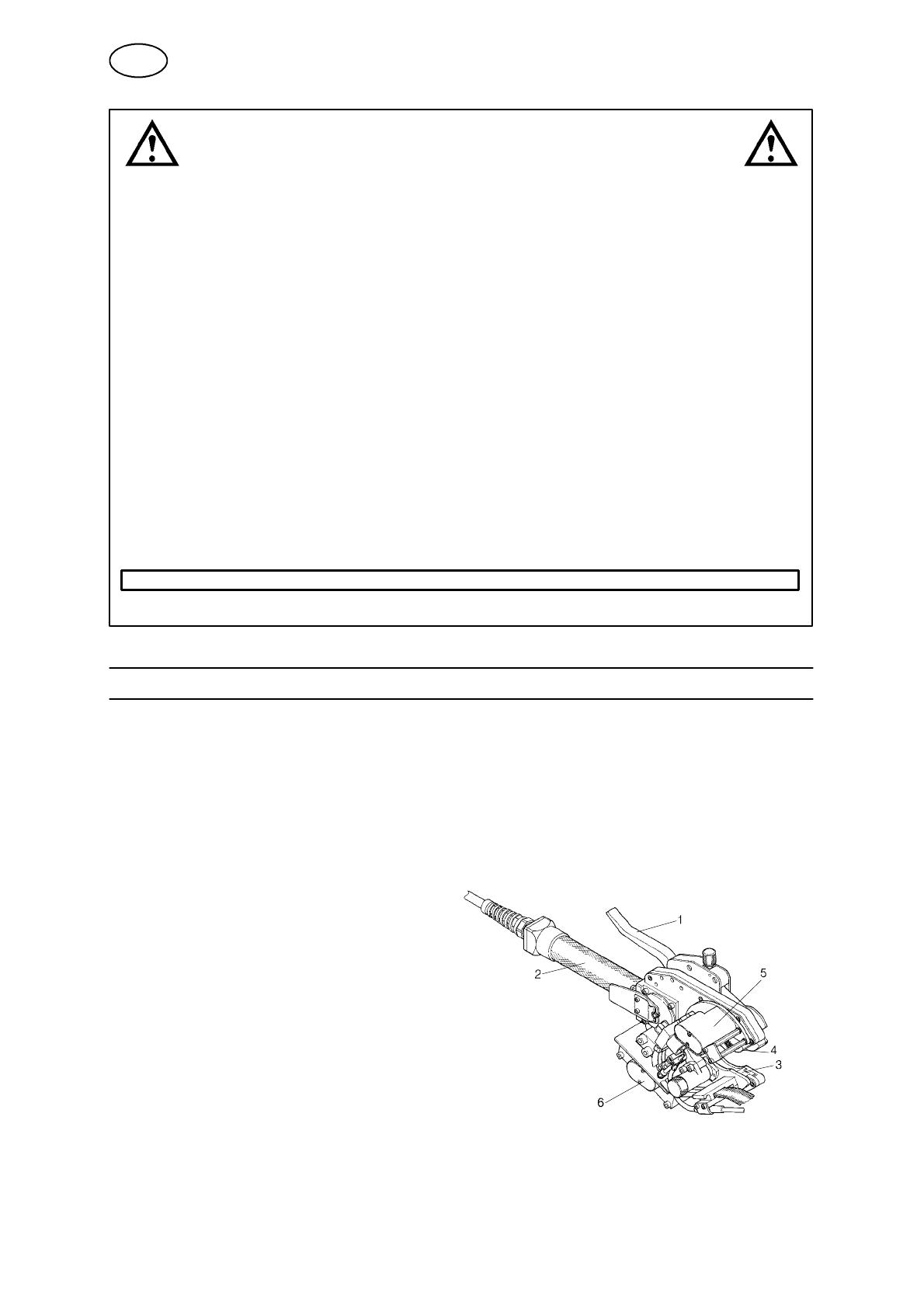
-- 2 0 --
dsa9d1ea
WARNING
READ AND UNDERSTAND THE INSTRUCTION MANUAL BEFORE INSTALLING OR OPERATING.
ARC WELDING AND CUTTING CAN BE INJURIOUS TO YOURSELF AND OTHERS. TAKE PRECAU -
TIONS WHEN WELDING. ASK FOR YOUR EMPLOYER’S SAFETY PRACTICES WHICH SHOULD BE
BASED ON MANUFACTURERS’ HAZARD DATA.
ELECTRIC SHOCK -- Can kill
S Install and earth the welding unit in accordance with applicable standards.
S Do not touch live electrical parts or electrodes with bare skin, wet gloves or wet clothing.
S Insulate yourself from earth and the workpiece.
S Ensure your working stance is safe.
FUMES AND GASES -- Can be dangerous to health
S Keep your head out of the fumes.
S Use ventilation, extraction at the arc, or both, to take fumes and gases away from your breathing zone
and the general area.
ARC RAYS -- Can injure eyes and burn skin.
S Protect y our eyes and body. Use the correct welding screen and filter lens and wear protective
clothing.
S Protect bystanders with suitable screens or curtains.
FIRE HAZARD
S Sparks (spatter) can cause fire. Make sure therefore that there are no inflammable materials nearby.
NOISE -- Excessive noise can damage hearing
S Protect y our ears. Use earmuffs or other hearing protection.
S Warn bystanders of the risk.
MALFUNCTION -- Call for expert assistance in the event of malfunction.
PROTECT YOURSELF AND OTHERS!
3 INTRODUCTION
A21 PRC 17--49 / 33--90 / 60--170 is designed for T IG welding of tube joints.
The tube welding tools are water--cooled and include weaving function (6) and
automatic arc length control (by control of the arc voltage = AVC) (5). The tools are
adapted for connection to the power source LTP 450. When filler wire is requir e d the
MEI 21 wire feed unit is to be used.
The tube welding tools incorporate a special gripping principle facilitating rapid and
accurate securing and location of the tool
on the tube. T he pair of gripping jaws (4)
clamp the tool to the tube when the
locking lever (1) on the handle is
pressed in. Only the gear collar (3) with
the fitted details rotates during welding.
The collar is powered by a drive unit (2)
consisting of a perm. magnet DC motor
and a pulse transmitter for speed
control. The motor is powered by the
control equipment (power source).
GB