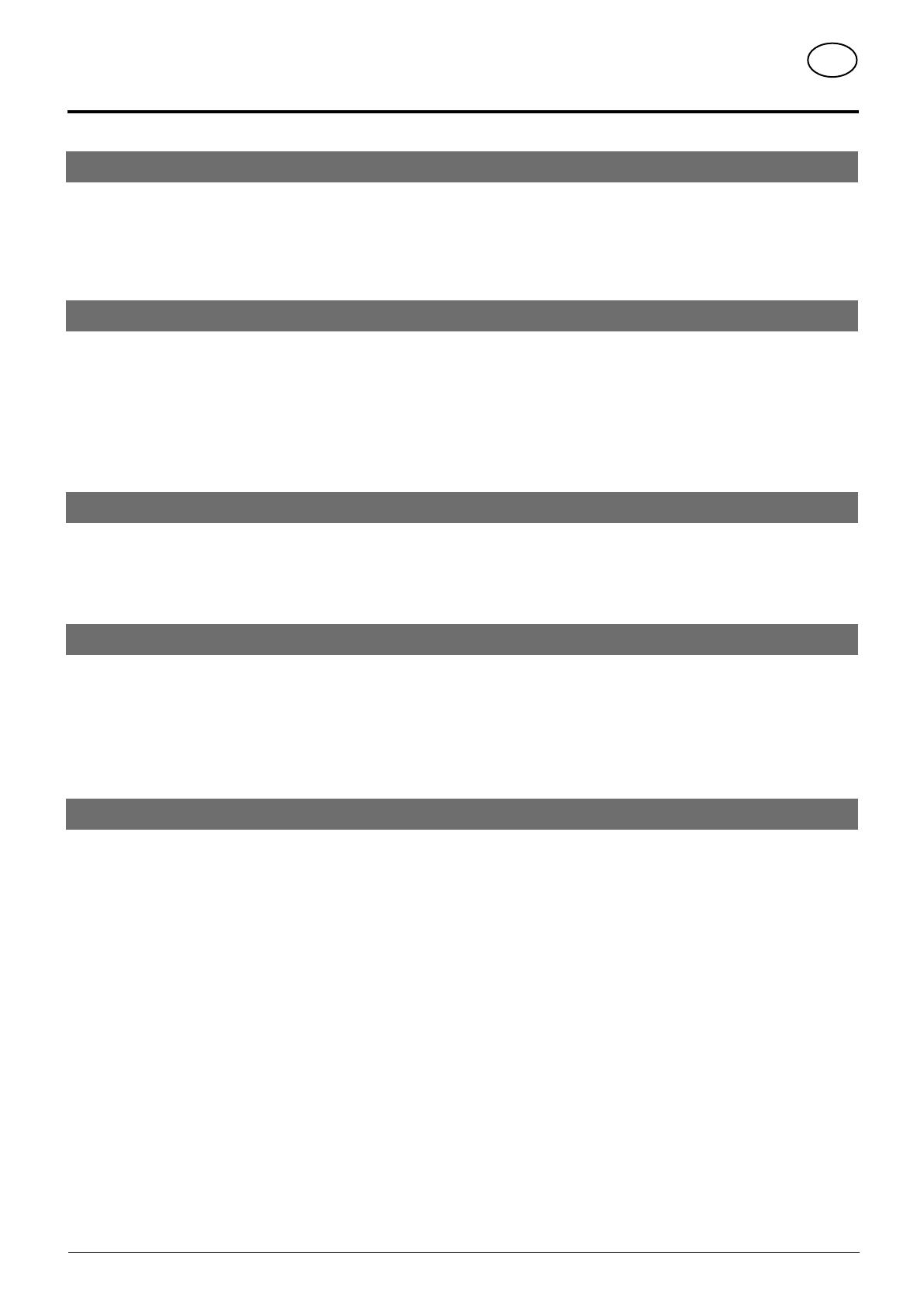
1200_GB-SICHERHEIT-AUTOCUT_548
GB
- 5 -
SAFETY HINTS
In general
Safety advice helps safeguard against physical and life threatening injuries and prevents damage through inappropriate use of the machine. For
those reasons read this manual carefully before initial operation and before working with or on the machine, and read and observe the safety
advice given in this manual as well as the illustrative safety warnings affixed to the machine.
The machine operator is fully responsible for injuries and damages caused as a result of not having followed this manual.
Personnel qualification
Only persons who have reached the minimum legal age, who are physically and intellectually suited and have had the appropriate training or
instruction may work with this machine.
Persons being trained or are learning or being instructed, or those in the framework of a general education may work on or with the machine
only under the constant supervision of an experienced person.
Checking, adjusting and repair work must only be carried out by authorised specialists.
Responsibility lies fully with the machine operator. Also to be observed are the applicable regional regulations.
Definition of use
The machine is designed to be used exclusively for grinding cutters. Any other use or use that goes beyond that is regarded as not being
consistent with the definition of use. The operator is fully liable for any damage resulting from such uses.
Observing the manual and heeding the maintenance requirements are also included in the definition of use.
Organizational measures
Retain the manual and keep it close at hand.
Observe general current, statutory and other binding regulations for accident prevention along with the advice in this manual. Such obligations
could include the wearing of personal protective gear or adhering to statutory traffic regulations.
Before starting work make yourself familiar with the function of all operating devices.
It is absolutely necessary to have an adequately equipped workshop in which to carry out checking, adjusting and repair work.
Adhering to operating safety
Only operate the machine when it is in technically perfect condition. Use only as per the defined use and be aware of safety and danger.
Immediately remove or have a specialist workshop remove all defects that impair safety or take the machine to a specialist workshop
Observe the illustrative warning signs affixed to the machine.
The operator must ensure that all illustrative warning signs are present and legible during the entire time the machine is in operation.
Do not undertake any unauthorised additions, modifications or alterations to the machine. This also applies to the installation and setting of
safety devices as well as welding or drilling in stress-bearing parts.
Spare parts, optional extras and additional devices must either be genuine Pöttinger parts or parts expressly released by Pöttinger. Such parts
have had their reliability, safety and suitability established especially for Pöttinger machines. We cannot evaluate other products and therefore
cannot vouch for them.
Maintenance work, as described in this manual, must be fully carried out at the given time intervals or have them completed in a specialist
workshop.
Do not make any software alterations to the programmable control system.