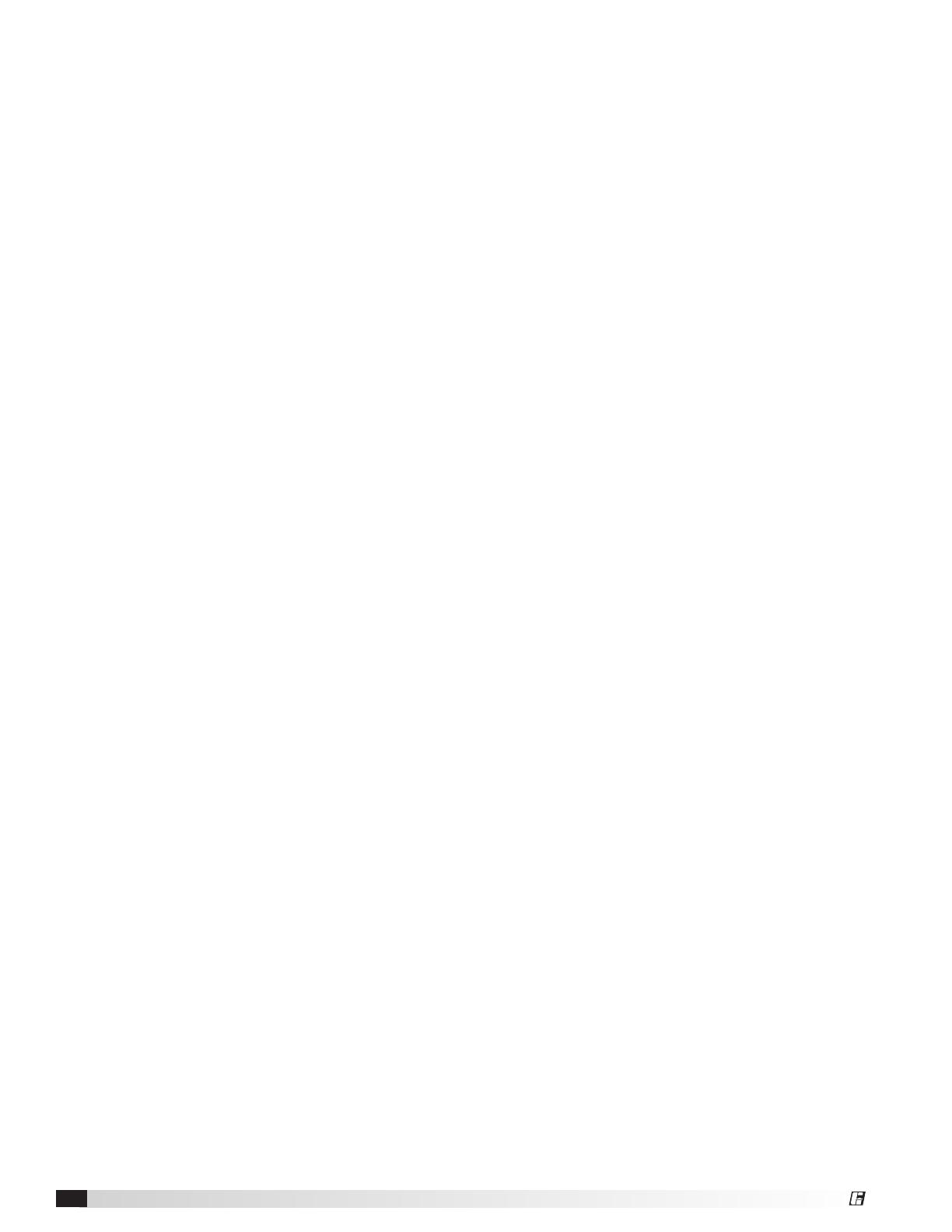
Belt Drive Duct Fan2
Receiving
Upon receiving the product, check to ensure all
items are accounted for by referencing the delivery
receipt or packing list. Inspect each crate or carton
for shipping damage before accepting delivery. Alert
the carrier of any damage detected. The customer will
make notification of damage (or shortage of items) on
the delivery receipt and all copies of the bill of lading
which is countersigned by the delivering carrier. If
damaged, immediately contact your Representative.
Any physical damage to the unit after acceptance
is not the responsibility of the manufacturer.
Unpacking
Verify that all required parts and the correct quantity
of each item have been received. If any items are
missing, report shortages to your local representative to
arrange for obtaining missing parts. Sometimes it is not
possible that all items for the unit be shipped together
due to availability of transportation and truck space.
Confirmation of shipment(s) must be limited to only items
on the bill of lading.
Handling
Move fan to desired location and determine position
of access panels and motor. Make sure inlet and
outlet have at least 2½ times the wheel diameter
(duct diameter) before any obstructions like an elbow
or transition. Attach the fan to a suitable framework
as specified, (hanging or base vibration isolators are
recommended). See Chart 1 on page 3 for physical
dimensions (Figure 1) and Chart 3 on page 3 for
dimensions of vibration isolators (Figure 3).
The motor’s amperage and voltage ratings must be
checked for compatibility to supply voltage prior to
final electrical connection. Supply wiring may be routed
through knockouts which are provided on the top and
bottom of each fan housing. Provide adequate wiring
to permit the access doors to open for servicing. Wiring
should be secured inside the fan to prevent interference
with the drive components. All wiring must conform to
local and national codes.
Storage
Fans are protected against damage during shipment. If
the unit cannot be installed and operated immediately,
precautions need to be taken to prevent deterioration of
the unit during storage. The user assumes responsibility
of the fan and accessories while in storage. The
manufacturer will not be responsible for damage during
storage. These suggestions are provided solely as a
convenience to the user.
Indoor - The ideal environment for the storage of fans
and accessories is indoors, above grade, in a low
humidity atmosphere which is sealed to prevent the entry
of blowing dust, rain or snow. Temperatures should be
evenly maintained between 30° to 110°F (-1° to 43°C)
(wide temperature swings may cause condensation
and “sweating” of metal parts). All accessories must be
stored indoors in a clean, dry atmosphere.
Remove any accumulations of dirt, water, ice or snow
and wipe dry before moving to indoor storage. To avoid
“sweating” of metal parts allow cold parts to reach room
temperature. To dry parts and packages use a portable
electric heater to get rid of any moisture buildup. Leave
coverings loose to permit air circulation and to allow for
periodic inspection.
The unit should be stored at least 3½ in. (89 mm) off the
floor on wooden blocks covered with moisture proof
paper or polyethylene sheathing. Aisles between parts
and along all walls should be provided to permit air
circulation and space for inspection.
Outdoor - Fans designed for outdoor applications may
be stored outdoors, if absolutely necessary. Roads or
aisles for portable cranes and hauling equipment are
needed.
The fan should be placed on a level surface to prevent
water from leaking into the fan. The fan should be
elevated on an adequate number of wooden blocks so
that it is above water and snow levels and has enough
blocking to prevent it from settling into soft ground.
Locate parts far enough apart to permit air circulation,
sunlight and space for periodic inspection. To minimize
water accumulation, place all fan parts on blocking
supports so that rain water will run off.
Do not cover parts with plastic film or tarps as these
cause condensation of moisture from the air passing
through heating and cooling cycles.
Fan wheels should be blocked to prevent spinning
caused by strong winds.
Inspection & Maintenance During Storage
While in storage, inspect fans once per month. Keep a
record of inspection and maintenance performed.
If moisture or dirt accumulations are found on parts,
the source should be located and eliminated. At each
inspection, rotate the wheel by hand ten to fifteen
revolutions to distribute lubricant on motor. If paint
deterioration begins, consideration should be given to
touch-up or repainting. Fans with special coatings may
require special techniques for touch-up or repair.
Machined parts coated with rust preventive should be
restored to good condition promptly if signs of rust
occur. Immediately remove the original rust preventive
coating with petroleum solvent and clean with lint-free
cloths. Polish any remaining rust from surface with
crocus cloth or fine emery paper and oil. Do not destroy
the continuity of the surfaces. Thoroughly wipe clean
with Tectyl
®
506 (Ashland Inc.) or the equivalent. For
hard to reach internal surfaces or for occasional use,
consider using Tectyl
®
511M Rust Preventive, WD-40
®
or the equivalent.
Removing From Storage
As fans are removed from storage to be
installed in their final location, they should be
protected and maintained in a similar fashion
until the fan equipment goes into operation.