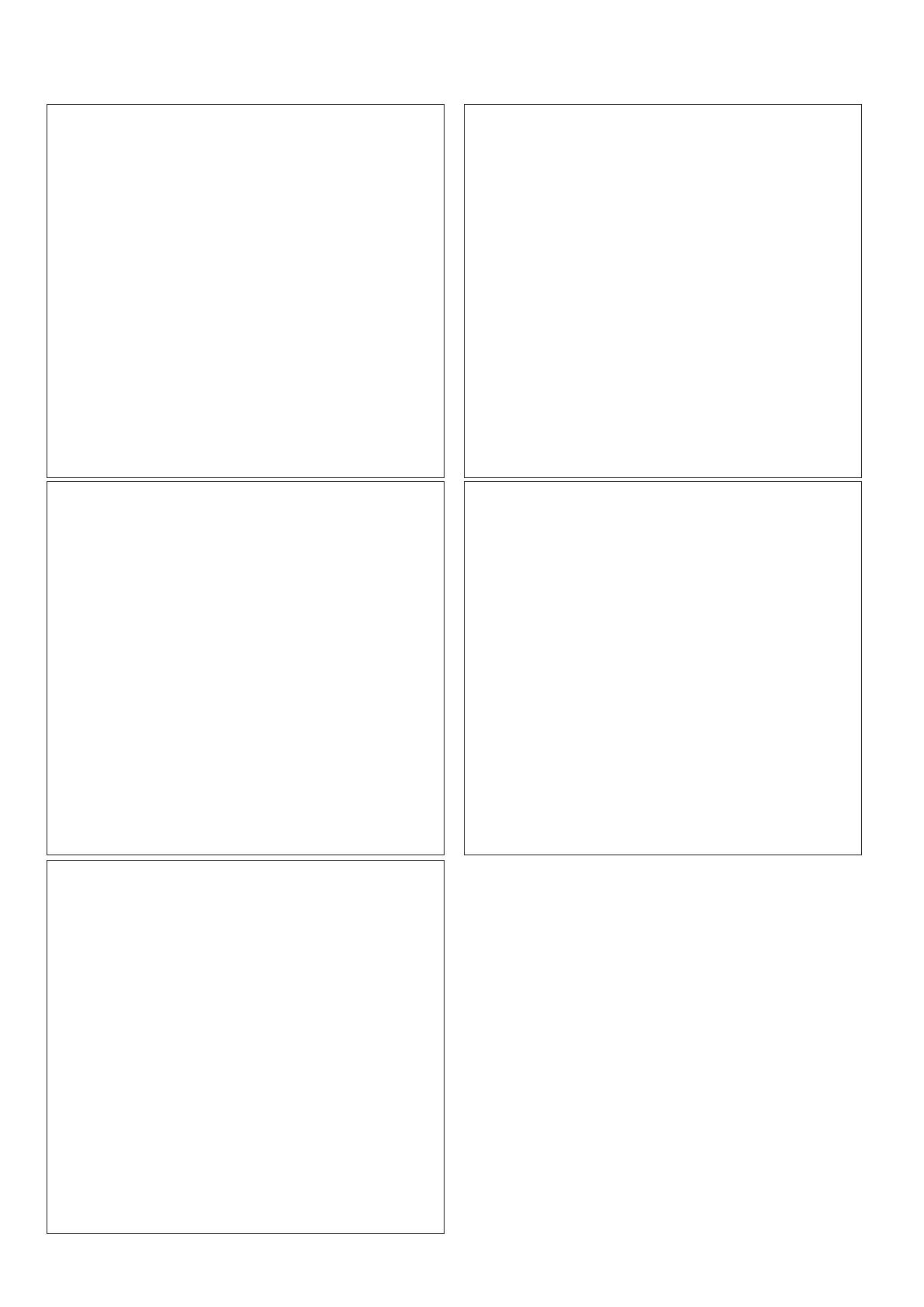
2 3ADW000395R0100 DCS550 Quick guide edisf a2 3ADW000395R0100 DCS550 Quick guide edisf a
DCS550 Quick Guide
english Contents
DC Drives Worldwide Service Network .............................. 3
DCS550 Manuals ............................................................... 4
DCS550 DC Drives ............................................................. 5
Brief instructions for CD and documents overview ............. 7
Notes on EMC .................................................................... 8
Standard function assignments for the terminals ............... 10
Connection example ......................................................... 11
Fan power connection ...................................................... 13
Terminal locations on the converter ................................... 14
Notes For North American Installations ............................. 15
Safety and operating instructions .....................................17
Installing the DCS550 PC tools on Your computer ............ 18
Commissioning .................................................................19
DCS550 Control Panel ..................................................... 20
Dimensions, drilling patterns and weights ........................ 77
Fault / Alarm list ............................................................... 80
Diagnosis messages.......................................... ...............86
Macro & Firmware structure .............................................. 91
Declaration of conformity ................................................ 104
Declaration of Incorporation ........................................... 105
deutsch Inhalt
DC Drives Worldwide Service Network .............................. 3
DCS550 Manuals / DCS550 Handbücher ........................... 4
DCS550 Gleichstromantriebe ........................................... 21
Kurzanweisung CD und Dokumentationsübersicht .......... 23
EMV Filter ......................................................................... 24
Digitaler und analoger E-A/Anschluss von SDCS-CON-F .. 26
Anschlussbeispiel .............................................................27
Lüfterkühlung ...................................................................29
Klemmen- und Steckeranordnung des Stromrichters ........ 30
Sicherheits- und Anwendungshinweise ............................. 31
Installation der DCS550 Programme auf dem PC ............. 32
Inbetriebnahme ................................................................33
DCS550 Steuertafel .......................................................... 34
Abmessungen, Bohrbild und Gewichte ............................ 77
Fehler- / Alarmliste ...........................................................80
Diagnosemeldungen.......................................... ............... 86
Makro & Firmware Struktur ...............................................91
Declaration of conformity ................................................ 104
Declaration of Incorporation ........................................... 105
italiano Indice
DC Drives Worldwide Service Network .............................. 3
DCS550 Manuals / DCS550 Manuali .................................. 4
DCS550 DC Drives ........................................................... 35
Brevi istruzioni CD e documentazione Panoramica ........... 37
Note sulle EMC .................................................................38
Assegnazione funzioni standard per i morsetti .................. 40
Esempi schemi di collegamento........................................41
Ventole di raffreddamento ................................................. 43
Posizioni terminali sul convertitore .....................................44
Istruzioni per la sicurezza .................................................. 45
Installa i DCS550 PC tools sul Tuo computer ....................46
Messa in servizio .............................................................. 47
DCS550 Pannello di controllo ........................................... 48
Dimensioni, schemi di foratura e pesi ...............................77
Errore / Allarme di lista ..................................................... 80
Messaggi di diagnostica.......................................... ......... 86
Struttura macro & firmware ............................................... 91
Declaration of conformity ................................................ 104
Declaration of Incorporation ........................................... 105
español Contenido
DC Drives Worldwide Service Network ............................... 3
DCS550 Manuals / Manuales de DCS550 .......................... 4
Convertidores de CC DCS550 ......................................... 49
Instrucciones para el CD y de la documentación .............. 51
Notas acerca de EMC ..................................................... 52
Asignaciones de funciones estándar para los terminales ... 54
Ejemplo de conexión ........................................................ 55
Conexión de alimentación del ventilador .......................... 57
Ubicación de los terminales en el convertidor ................... 58
Instrucciones de seguridad ............................................... 59
Cómo instalar las herramientas para PC del DCS550 ......60
Puesta en funcionamiento ............................................... 61
Panel de control del DCS550 ........................................... 62
Dimensiones, patrones de taladrado y pesos....................77
Lista de errores / alarmas ................................................ 80
Mensajes de diagnóstico ................................................. 86
Estructura del macro & firmware ....................................... 91
Declaration of conformity ................................................ 104
Declaration of Incorporation ............................................ 105
français Sommaire
DC Drives Worldwide Service Network .............................. 3
DCS550 Manuals / Manuels du DCS550 ............................ 4
Variateurs à courant continu DCS550 ............................... 63
Documentation technique ................................................65
Compatibilité électromagnétique (CEM) ............................ 66
Raccordement standard des signaux d’E/S ...................... 68
Exemple de schéma de câblage ....................................... 69
Câblage du ventilateur ...................................................... 71
Emplacement des bornes sur le convertisseur .................. 72
Consignes de sécurité et d’exploitation............................. 73
Installation des outils logiciels du DCS550 sur votre PC ....74
Mise en service ................................................................. 75
Micro-console DCS550 .................................................... 76
Dimensions, perçages et poids ........................................77
Liste des erreurs / alarmes ............................................... 80
Messages de diagnostic.......................................... ......... 86
Structure du logiciel macro & système .............................. 91
Declaration of conformity ................................................ 104
Declaration of Incorporation ........................................... 105