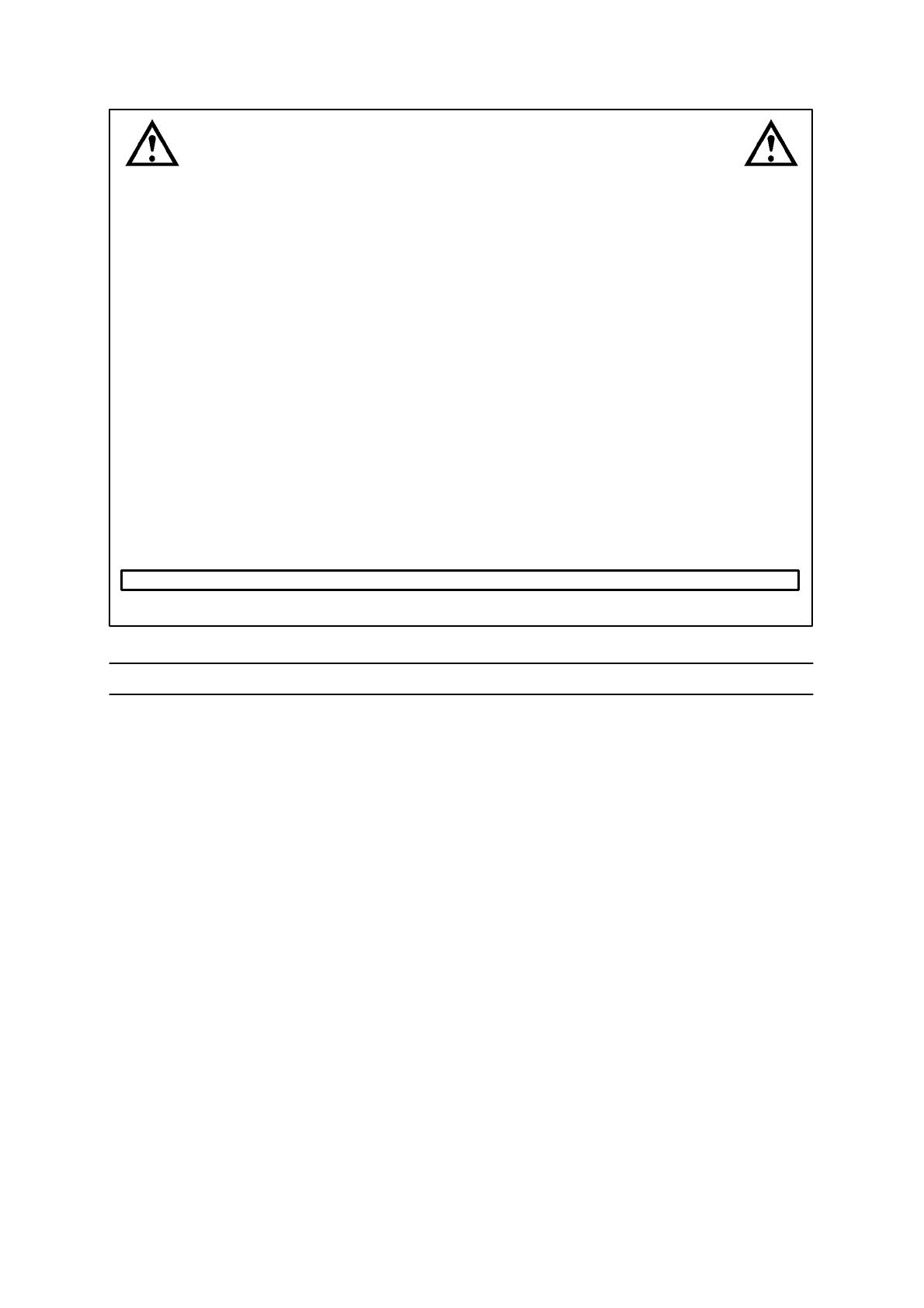
-- 1 2 --
doce
WARNING
READ AND UNDERSTAND THE INSTRUCTION MANUAL BEFORE INSTALLING OR OPERATING.
ARC WELDING AND CUTTING CAN BE INJURIOUS TO YOURSELF AND OTHERS. TAKE PRECAU-
TIONS WHEN WELDING. ASK FOR YOUR EMPLOYER’S SAFETY PRACTICES WHICH SHOULD BE
BASED ON MANUFACTURERS’ HAZARD DATA.
ELECTRIC SHOCK -- Can kill
S Install and earth the welding unit in accordance with applicable standards.
S Do not touch live electrical parts or electrodes with bare skin, wet gloves or wet clothing.
S Insulate yourself from earth and the workpiece.
S Ensure your working stance is safe.
FUMES AND GASES -- Can be dangerous to health
S Keep your head out of the fumes.
S Use ventilation, extraction at the arc, or both, to keep fumes and gases from your breathing zone and
the general area.
ARC RAYS -- Can injure eyes and burn skin.
S Protect your eyes and body. Use the correct welding screen and filter lens and wear protective
clothing.
S Protect bystanders with suitable screens or curtains.
FIRE HAZARD
S Sparks (spatter) can cause fire. Make sure therefore that there are no inflammable materials nearby.
NOISE -- Excessive noise can damage hearing
S Protect your ears. Use ear defenders or other hearing protection.
S Warn bystanders of the risk.
MALFUNCTION -- Call for expert assistance in the event of malfunction.
PROTECT YOURSELF AND OTHERS!
2 INTRODUCTION
2.1 General
TAF 800/1250 are remotely controlled, two --phase AC welding power sources
designed for high--throughput, mechanised submerged--arc welding. They should
always be used in conjunction with ESAB’s control box A2--A6 Process Controller
(PEH).
The welding power source converts, via a thyristor bridge--rectifier, the secondary
voltage’s sine wave to a square wave with excellent arc ignition and welding
characteristics. They are fan cooled and are overload protected by a thermal
cut--out. Re --setting takes place automatically as soon as the temperature has
reduced to an acceptable level.
The welding power source and control box are connected together via a two--wire
bus, which makes it possible to control the welding process very precisely.
Adjustment of the welding power source can be carried out from the front panel of
the control box, where all the welding parameters can be adjusted by the operator.
The operation of the welding power source is controlled and monitored completely
by the control box, from which the start and stop characteristics can be set. The
pre--set welding parameters can be monitored while welding is in progress.
For detailed information about remote control, please refer to the instruction manual
for the A2--A6 Process Controller.