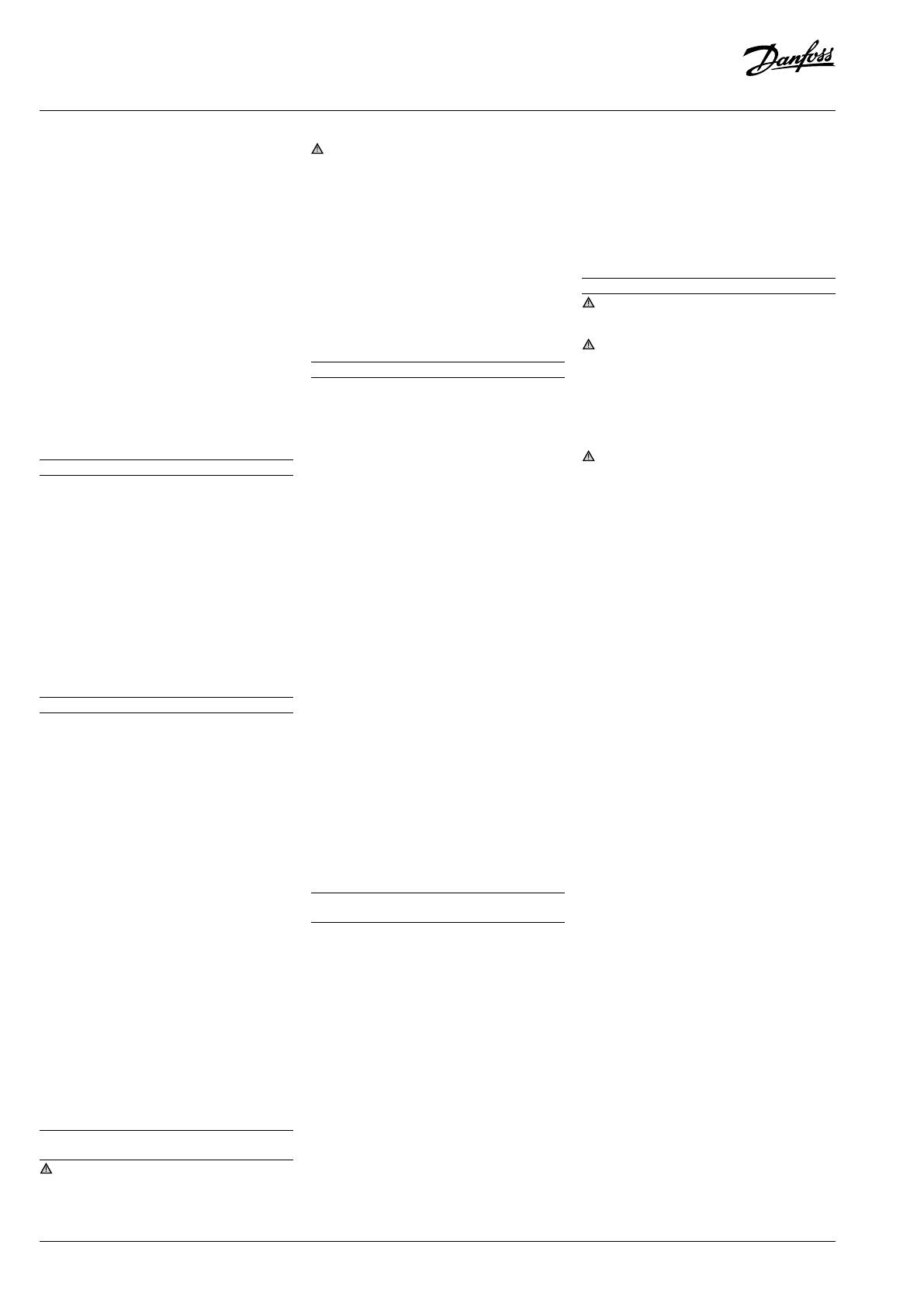
Anleitung
© Danfoss | Climate Solutions | 2022.02
14 | AN23308644013405-001701 - 118A0549G
• Die Einheit ist mit Hoch- und Niederdruckschal-
tern ausgestattet, die bei Aktivierung die Versor-
gungsspannung des Verdichters direkt unter-
brechen und 230-V-Wechselstrom-Alarmsignale
ausgeben (max. 50 VA). Parameter für Hoch- und
Niederdruckbegrenzungen müssen durch den
Installateur vorgenommen werden, unter Be-
rücksichtigung von Verdichtermodell, Kältemit-
tel und Anwendungsbereich. Produkte mit Dan-
foss MLZ- und LLZ- Verdichtern sind auch mit
Phasenfolgerelais ausgestattet, um das Produkt
gegen Phasenverlust/falsche Phasenfolge/
Asymmetrie und Über-/Unterspannung zu
schützen.
Bei Anlagen mit einem 3-Phasen-Scrollverdichter
(OP-SMLZxxxxxxxxE) muss die korrekte Phasense-
quenz für die Drehrichtung des Verdichters be-
achtet werden.
• Ermitteln Sie die Phasensequenz mit einem Pha-
senmesser, um die Phasenreihenfolge der Lei-
tungsphasen L1, L2 und L3 festzustellen.
• Schließen Sie die Leitungsphasen L1, L2 und L3
an die entsprechenden Hauptschalterklemmen
T1, T2 und T3 an.
8 – Sicherheit
Ein Sicherungsstecker ist in der Einheit nicht
verfügbar, an seiner Stelle befindet sich ein
Adapterstecker.
Die Einheit verfügt über einen
Flüssigkeitssammler mit Adapterstecker mit 3/8”
NPT-Anschluss. Installateure/Endverbraucher
können verschiedene Optionen auswählen
gemäß EN 378-2: 2016 Artikel § 6.2.2.3
• Die Kälteanlage, in die der Verflüssigungssatz
integriert wird, muss der Druckgeräterichtlinie
entsprechen.
• Vorsicht vor heißen und kalten Oberflächen.
• Achten Sie auf bewegliche Komponenten.
Während der Wartung muss die
Versorgungsspannung getrennt sein.
9. Füllen der Anlage
• Tragen Sie Schutzkleidung wie z. B. eine Schutz-
brille und Schutzhandschuhe.
• Nehmen Sie den Verdichter niemals unter Vaku-
um in Betrieb. Sorgen Sie dafür, dass der Ver-
dichter ausgeschaltet ist und nicht plötzlich aus-
pringt.
• Vor dem Auswechseln des Kältemittels muss si-
chergestellt sein, dass das Ölniveau im Schau-
glas des Verdichters zwischen ¼ und ¾ liegt.
Sollte zusätzlich Öl benötigt werden, entneh-
men Sie die nötigen Informationen über das er-
forderliche Öl bitte dem Tapenschild des Ver-
dichters.
• Verwenden Sie ausschließlich das Kältemittel,
auf das der Verflüssigungssatz ausgelegt ist.
• Füllen Sie das flüssige Kältemittel in den Verflüs-
siger oder Sammler. Stellen Sie sicher, dass die
Anlage langsam befüllt wird (auf 4 bis 5 bar bei
R404A/R507A/R407A/R407F/R448A/R449A /
R452A und auf ca. 2 bar bei R134a/R513A).
• Das Kältemittel darf nicht in die Saugleitung ge-
langen.
• Dem Öl/Kältemittel dürfen keine Zusätze beige-
mischt werden.
• Die Anlage wird dann weiter befüllt, bis die Instal-
lation
beim Betrieb einen stabilen Nennzustand
erreicht hat.
• Lassen Sie den Einfüllstutzen niemals an den
Kreislauf angeschlossen.
10. Abschließende Prüfung vor der Inbetrieb-
nahme
Verwenden Sie gemäß den allgemeinen und
landesspezifischen Sicherheitsnormen und -vor-
schriften Sicherheitsvorrichtungen wie Sicher-
heitsdruckschalter und mechanische Überdruck-
ventile. Vergewissern Sie sich, dass diese
Sicherheitsvorrichtungen funktionstüchtig und
ordnungsgemäß eingestellt sind.
Überprüfen Sie, dass die Einstellungen für die
Hochdruckschalter und Überdruckventile den
maximalen Betriebsdruck jeglicher Bauteile der
Anlage nicht überschreiten.
• Vergewissern Sie sich, dass sämtliche elektri-
schen Anschlüsse ordnungsgemäß befestigt
sind und den Vorschriften Ihres Landes entspre-
chen.
• Wenn eine Kurbelwannenheizung erforderlich
ist, muss diese mindestens 12 Stunden vor der
ersten Inbetriebnahme der Anlage eingeschal-
tet werden. Dies gilt auch vor einer erneuten In-
betriebnahme nach einer längeren Stillstands-
zeit.
11. Inbetriebnahme
• Die Anlage darf keinesfalls ohne Kältemittel ge-
startet oder betrieben werden.
• Alle Serviceventile müssen geöffnet sein. Siehe
Abb. 3.
• Überprüfen Sie, ob die vorhandene Versor-
gungsspannung mit dem erforderlichen Wert
für den Verflüssigungssatz übereinstimmt.
• Überprüfen Sie, ob die Kurbelwannenheizung
funktioniert.
• Überprüfen Sie, ob sich der Lüfter frei drehen
kann.
• Überprüfen Sie, ob die Schutzfolie auf der Rück-
seite des Verflüssigers entfernt wurde.
• Nehmen Sie einen Ausgleich zwischen Hoch-
und Niederdruckseite vor.
• Schalten Sie den Verflüssigungssatz ein. Der Ver-
flüssigungssatz muss sofort anlaufen. Falls der
Verdichter nicht anläuft, überprüfen Sie die Ver-
drahtung und die Spannung an den Klemmen.
• Ob sich ein 3-Phasen-Scrollverdichter in die Ge-
genrichtung dreht, lässt sich an folgenden Phä-
nomenen erkennen: Der Verdichter ist mit ei-
nem Phasenumkehr-Relais ausgestattet, läuft
nicht an und baut keinen Druck auf. Der Verdich-
ter arbeitet mit einem ungewöhnlichen hohen
Geräuschpegel. Die Leistungsaufnahme des Ver-
dichters ist ungewöhnlich gering. Bei falscher
Drehrichtung des Verdichters muss der Verdich-
ter sofort abgeschaltet werden, um die Lei-
tungsphasen an die korrekten Klemmen anzu-
schließen.
• Bei korrekter Drehrichtung ist an der Nieder-
druckanzeige bzw. am Niederdruckmanometer
ein sinkender Druck abzulesen – und an der
Hochdruckanzeige bzw. am Hochdruckmano-
meter ein steigender Druck.
12. Überprüfung bei laufendem Verflüssigungs-
satz
• Überprüfen Sie die Drehrichtung des Lüfters. Die
Luft muss vom Verflüssiger zum Lüfter strömen.
• Überprüfen Sie Stromaufnahme und Spannung.
• Überprüfen Sie die Überhitzung der Sauglei-
tung, um das Risiko von Flüssigkeitsschlägen zu
vermindern.
• Sofern ein Schauglas vorhanden ist, beobachten
Sie den Ölstand beim Anlaufen und während
des Betriebs, um sicherzustellen, dass der Öl-
stand sichtbar bleibt.
• Beachten Sie die Betriebsgrenzen.
• Überprüfen Sie alle Leitungen auf übermäßige
Vibrationen. Bewegungen von mehr als 1,5 mm
erfordern Korrekturmaßnahmen wie z. B. die
Verwendung von Rohrhalterungen.
• Ggf. kann auf der Niederdruckseite in größt-
möglichem Abstand zum Verdichter flüssiges
Kältemittel nachgefüllt werden. Während dieses
Nachfüllvorgangs muss der Verdichter in Betrieb
sein.
• Überfüllen Sie die Anlage nicht.
• Beachten Sie die in Ihrem Land geltenden Vor-
schriften zum Recycling des Kältemittels aus
dem Gerät.
• Lassen Sie niemals Kältemittel in die Atmosphä-
re entweichen.
• Führen Sie eine allgemeine Inspektion der In-
stallation hinsichtlich Sauberkeit, Geräuschpe-
gel und Lecks durch, bevor Sie den Installations-
ort verlassen.
• Dokumentieren Sie die Art und Menge des Käl-
temittels sowie die Betriebsbedingungen als
Referenz für künftige Inspektionen.
13. Wartung
Schalten Sie den Verflüssigungssatz immer mit
dem Hauptschalter aus, bevor Sie die Lüftertür
öffnen.
Der in der Anlage herrschende Druck und die
Oberflächentemperatur können dauerhafte kör-
perliche Schäden verursachen.
Die Bediener, Installateure und Wartungstechni-
ker müssen dementsprechend geschult und aus-
gerüstet sein. Die Temperatur der Rohrleitungen
kann 100 °C
überschreiten und schwere Verbren-
nungen verursachen.
Stellen Sie sicher, dass regelmäßig Servicein-
spektionen gemäß den Vorschriften Ihres Landes
durchgeführt werden, um einen zuverlässigen
Betrieb der Anlage zu gewährleisten.
Um systembedingte Probleme zu vermeiden,
werden
die folgenden regelmäßigen Wartungsarbeiten
empfohlen:
• Vergewissern Sie sich, dass die Sicherheitsvor-
richtungen funktionstüchtig und ordnungsge-
mäß eingestellt sind.
• Stellen Sie sicher, dass keine Lecks in der Anlage
vorhanden sind.
• Überprüfen Sie die Stromaufnahme des Verdich-
ters.
• Vergewissern Sie sich anhand der Wartungsun-
terlagen, dass die Anlage entsprechend den bis-
herigen Werten und Betriebsbedingungen läuft.
• Überprüfen Sie, ob sämtliche elektrischen An-
schlüsse noch ordnungsgemäß befestigt sind.
• Sorgen Sie dafür, dass der Verflüssigungssatz sau-
ber ist und bleibt, und vergewissern Sie sich, dass
die Bauteile des Verflüssigungssatzes, die Rohre
und die
elektrischen Anschlüsse frei von Rost und
Oxidation sind
.
Der Verflüssiger muss mindestens einmal im Jahr
auf Verschmutzungen überprüft und ggf. gereinigt
werden. Ins Innere des Verflüssigers gelangen Sie
über die Lüftertür. Bei Microchannel-Wärmeüber-
tragern lagert sich der Schmutz eher auf als im Ver-
flüssiger. Deshalb sind sie leichter zur reinigen als
Kupferrohr-Lamellenverflüssiger.
• Schalten Sie den Verflüssigungssatz mit dem
Hauptschalter aus, bevor Sie ein Panel der Einheit
entfernen.
• Entfernen Sie oberflächlichen Schmutz, Blätter,
Fasern usw. mit einem Staubsauger mit Bürsten-
aufsatz bzw. mit einem anderen weichen Auf-
satz. Alternativ hierzu können Sie auch Druckluft
von innen nach außen durch das Register blasen
und mit einer weichen Bürste abbürsten. Ver-
wenden Sie keine Drahtbürste. Stoßen Sie nicht
mit dem Rohr oder der Düse des Staubsaugers
gegen die Spule und vermeiden Sie Kratzer.
Falls der Kältemittelkreislauf geöffnet wurde,
muss die Anlage mit trockener Luft oder Stickstoff
„gespült“ werden, um jegliche Feuchtigkeit zu
entfernen. Zudem muss ein neuer Filtertrockner
eingebaut werden. Falls eine Evakuierung des
Kältemittels erforderlich sein sollte, muss diese so
vorgenommen werden, dass kein Kältemittel in
die Umwelt entweicht.
Entnahme des Anschlusskasten der Version W09.