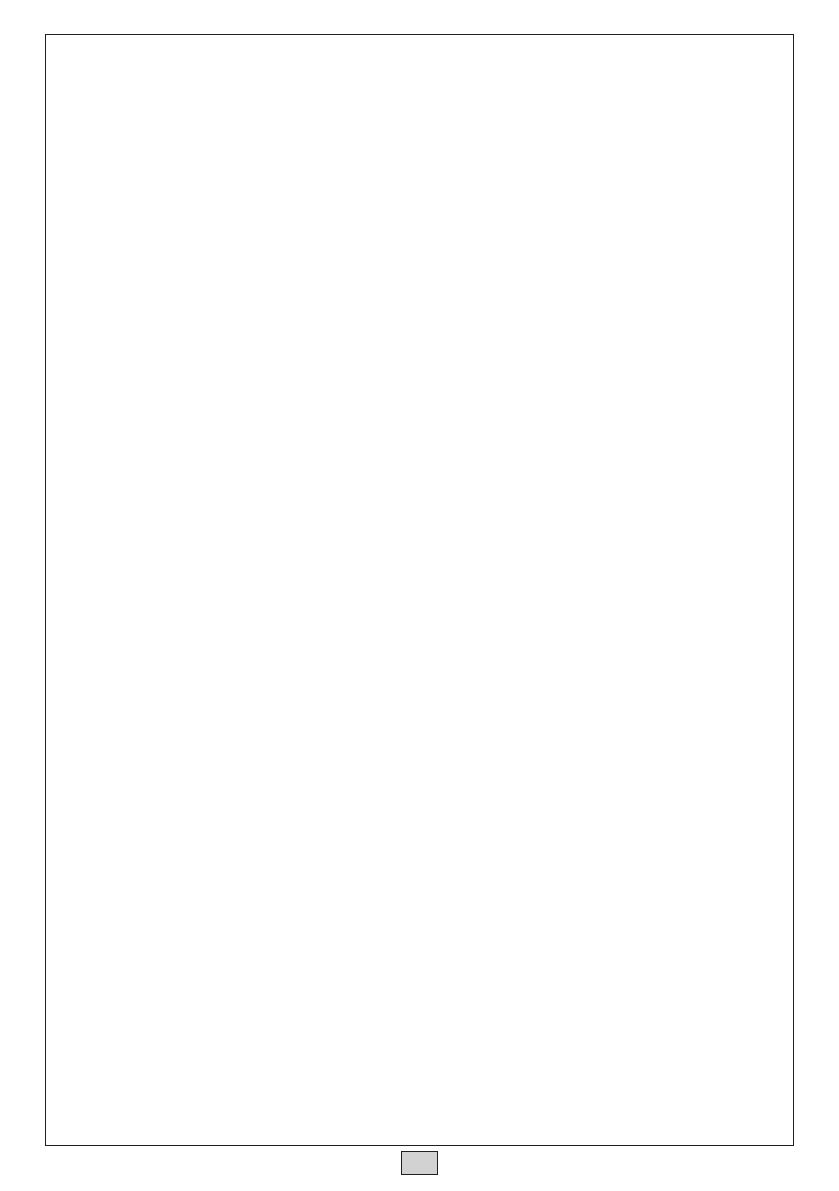
3 / 28 6-1622396 rev. 0
ENG
1. GENERAL SAFETY WARNINGS
ATTENTION - FOR THE SAFETY OF PEOPLE IT IS IMPORTANT TO FOLLOW ALL THE INSTRUCTIONS
KEEP THESE INSTRUCTIONS WITH CARE
1° - If it is not forecast in the electric gearcase, install a switch of magneto thermic type upstream, (omni polar with minimum
opening of the contacts of 3 mm) with a check of conformity to the international standards. Such device must be protected against
the accidental lockup (for example by installing inside a locked board).
2° - For the section and the type of the cables ALLMATIC advices to use a cable of H05RN-F type with 1,5 sqmm minimum section
and, however, to keep to the IEC 364 and installation standards in force in your country.
3° - Positioning of a possible couple of photoelectric cells: the radius of the photoelectric cells must be at a height of no more than
70 cm from the ground and at a distance not superior to 20 cm from the motion plane of the door. Their correct working must be
verified at the end of the installation in accordance with the point 7.2.1 of the EN 12445
4° - To fulfill the limits set by EN 12453, and in case the peak force exceeds the normative limit of 400 N it is necessary to have
recourse to the active presence survey on the whole height of the door (up to max 2,5 m) - The photoelectric cells, in this case, must
be applied in accordance with the point 7.3.2.2 of the EN 12445.
N.B.: The earthing of the system is obligatory.
The data described in this handbook are purely a guide.
ALLMATIC reserves the right to change them in any moment.
Carry out the system in the respect of the standards and laws in force.
IMPORTANT SAFETY INSTRUCTIONS FOR THE INSTALLATION
ATTENTION - THE INCORRECT INSTALLATION CAN CAUSE SERIOUS DAMAGES
FOLLOW ALL INSTALLATION INSTRUCTIONS
1° - This handbook is exclusively addressed to the specialized personnel who knows the constructive criteria and the
protection devices against accidents for motorized gates, doors and main doors (follow the standards and the laws in force).
2° - The installer will have to issue a handbook to the final user in accordance with the 12635.
3° - Before proceeding with the installation, the installer must forecast the risks analysis of the final automatized closing and the
safety of the identified dangerous points (Following the standards EN 12453/EN 12445).
4° - Before installing the motion motor, the installer must verify that the gate is in good mechanical conditions and that it adequately
opens and closes.
5° - The installer must install the member for the manual release at a height inferior to 1,8 m.
6° - The installer will have to remove possible impediments to the motorized motion of the gate (eg. door bolts, sliding bolts, door
locks etc.)
7° - The installer will permanently have to put the tags warning against the deflection on a very visible point or near possible fixed
controls.
8° - The wiring harness of the dierent electric components external to the operator (for example photoelectric cells, flashlights etc.)
must be carried out according to the EN 60204-1 and the modifications to it done in the point 5.2.2 of the EN 12453.
9° - The possible assembly of a keyboard for the manual control of the movement must be done by positioning the keyboard so
that the person operating it does not find himself in a dangerous position; moreover, the risk of accidental activation of the buttons
must be reduced.
10° - Keep the automatism controls (push-button panel, remote control etc.) out of the children way. Command device for operating
the motor (a switch manually closed) should be placed in area visible from the guided site and far from moving parts. It should be
placed at least at 1,5 m height.
11° - this appliance can be used by children aged from 8 years and above and persons with reduced physical, sensory or mental
capabilities or lack of experience and knowledge if they have been given supervision or instruction concerning use of the appliance
in a safe way and understand the hazards involved
12° - children shall not play with the appliance
13° - cleaning and user maintenance shall not be made by children without supervision
14° - do not allow children to play with fixed controls. Keep remote controls away from children
15° - Fixed command devices should be installed in a well visible way.
16° - Before carrying out any installation, regulation or maintenance operation of the system, take o the voltage by operating on
the special magneto thermic switch connected upstream.
17° - At the end of the installation, the installer will have to make sure that the parts of the
door do not encumber streets or public sidewalks.
THE ALLMATIC COMPANY DOES NOT ACCEPT ANY RESPONSIBILITY for possible damages caused by the non observan-
ce during the installation of the safety standards and of the laws in force at present.