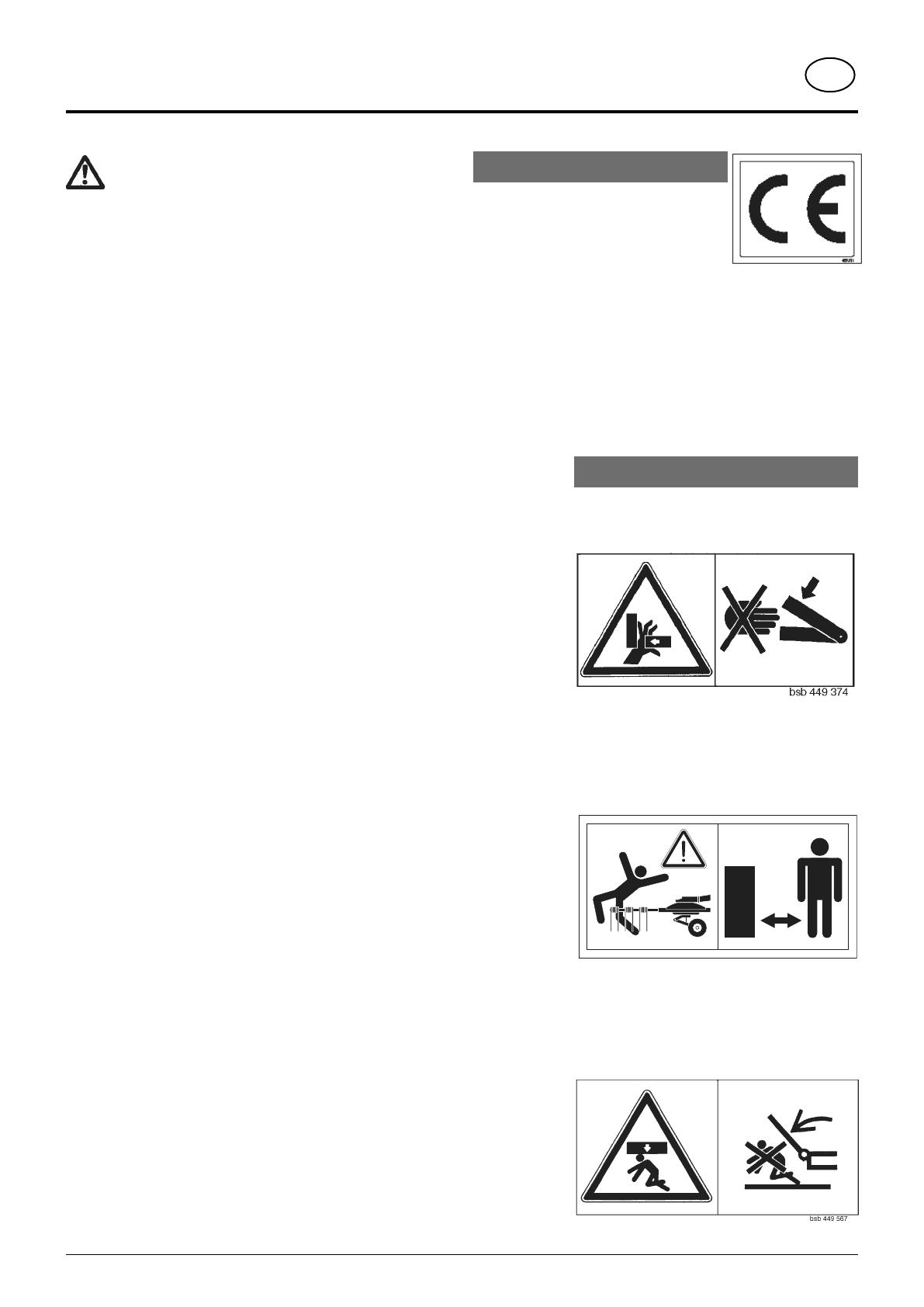
- 4 -
TABLE OF CONTENTS GB
?'").(!,4?
Observe Safety Hints in the supplement!
CE sign
The CE sign, which is affixed by the manufacturer,
indicates outwardly that this machine conforms
to the engineering guideline regulations and the
other relevant EU guidelines.
EU Declaration of Conformity
By signing the EU Declaration of Conformity, the manufacturer declares
that the machine being brought into service complies with all relevant
safety and health requirements.
Meaning of warning signs
Never reach into the crushing danger area as long
as parts may move.
Do not enter rotor area while driving motor is
running.
495.173
Stay clear of swinging area of implements
Table of Contents
Hitching of machines with three point linkage ........................ 5
Locking the headstock during use on roads and when lowe-
ring ........................................................................................ 5
Release rope .......................................................................... 5
Hitching ................................................................................. 6
of machines with pivoting drawbar ......................................... 6
Distance (X) adjustment ......................................................... 6
Release rope .......................................................................... 6
Driving on public roads: .......................................................... 8
Conversion from working to transport position ....................... 9
Attention! ............................................................................... 9
The order of operation must be adhered to. ........................... 9
Locking the headstock during use on roads : ........................ 9
Conversion from transport to working position ..................... 10
Attention! The order of operation must be adhered to. ......... 10
General guidelines for working with the machine ................. 11
Beware! ............................................................................... 11
Operating on slopes ............................................................. 11
Adjustment to implements with three-point-linkage: ............. 11
Adjustment to implements with pivoting drawbar: ................ 11
Setting lower link: ............................................................... 11
P.t.o. speed ........................................................................... 11
Tractor control device (ST) ................................................... 11
Tine adjustment .................................................................... 11
Clearing field edges (border tedding) to the left or to the right ........ 12
Anti-vibration braces ............................................................. 13
Remedy for noisy machine running ...................................... 13
Turning manœuvre in working position ................................ 13
Attention! The order of operation must be adhered to. ......... 13
Machines with pivoting drawbar ........................................... 13
Lowering the rotary tedder ................................................... 14
Lowering the machine .......................................................... 14
Cleaning of machine parts .................................................... 14
Parking in the open .............................................................. 14
Winter storage ...................................................................... 14
Maintenance and servicing ................................................... 15
Intake transmission .............................................................. 15
Changing tines ..................................................................... 15
Gas container ....................................................................... 15
Note ...................................................................................... 15
Alteration of gas container pressure ..................................... 15
MAINTENANCE ................................................................... 15
Warntafeln ............................................................................ 16
Tableau de signalisation ....................................................... 16
Warning plates ...................................................................... 16
Removable lightning ............................................................ 16
Technical data ...................................................................... 18
The defined use of the rotary tedder .................................... 18
Lubrication chart ................................................................ 21
Recommendations for work safety ...................................... 23
DRIVESHAFT ....................................................................... 24