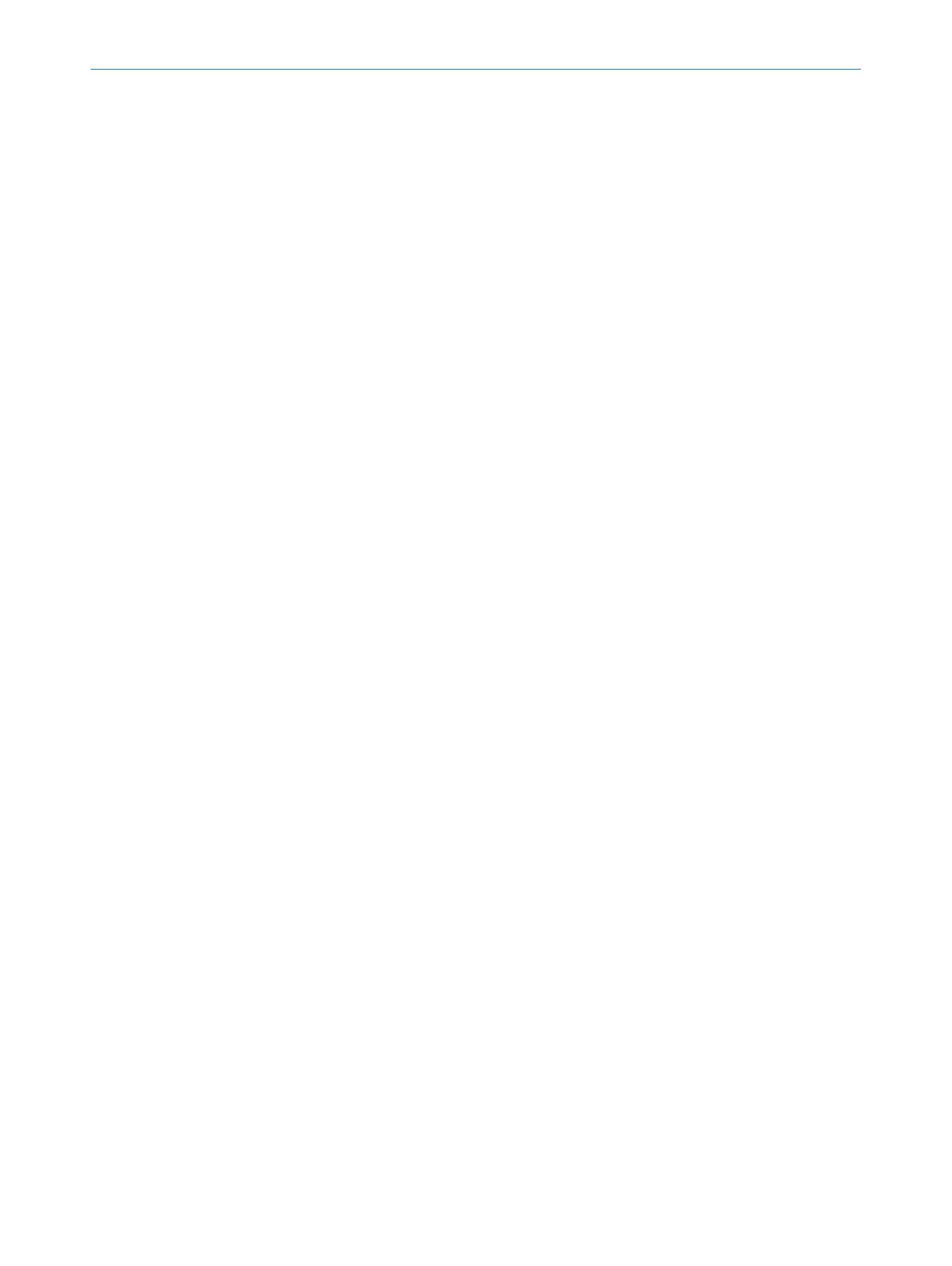
2 Safety information
2.1 General safety note
The information and tools will not fulfill the safety requirements for your application
w
ithout further adjustments being made. The project planning provided by way of
example is intended to serve as the basis to allow you to perform your own project
planning and programming in line with your specific requirements. What this means is
that the information and tools merely provide an example to demonstrate how a safety
function can be taken care of.
When it comes to your own project planning and programming, you will need to rely
on qualified staff given that it is your responsibility to ensure that the following require‐
ments are complied with at the very least:
b
Carrying out a risk assessment
b
Taking into account applicable standards
b
Verifying and validating the safety functions.
2.2 Intended use
The safety system is used to carry out a sub-safety function for automated guided vehi‐
c
les and transport carts (AGVs and AGCs). It protects, by means of mobile hazardous
area protection, the hazardous area created by the movement of an automated guided
vehicle.
The safety system is an example application and must be independently implemented
and validated.
The safety system must only be used within the limits of the prescribed and specified
technical data and operating conditions at all times.
Incorrect use, improper modification or manipulation of the safety system will invalidate
any warranty from SICK; in addition, any responsibility and liability of SICK for damage
and secondary damage caused by this are excluded.
2.3 Requirements for the qualification of personnel
The protective device must be planned in, installed, connected, commissioned, and
ser
viced by qualified safety personnel only.
Project planning
For project planning, a person is considered competent when he/she has expertise and
experience in the selection and use of protective devices on machines and is familiar
with the relevant technical rules and national work safety regulations.
Mechanical mounting, electrical installation, and commissioning
F
or the task, a person is considered qualified when he/she has the expertise and
experience in the relevant field and is sufficiently familiar with the application of the
protective device on the machine to be able to assess whether it is in an operationally
safe state.
Operation and maintenance
F
or operation and maintenance, a person is considered competent when he/she has
the expertise and experience in the relevant field and is sufficiently familiar with the
application of the protective device on the machine and has been instructed by the
machine operator in its operation.
2 S
AFETY INFORMATION
6
O P E R A T I N G I N S T R U C T I O N S | Safe AGV Easy 8026188/1BD7/2021-03-25 | SICK
Subject to change without notice