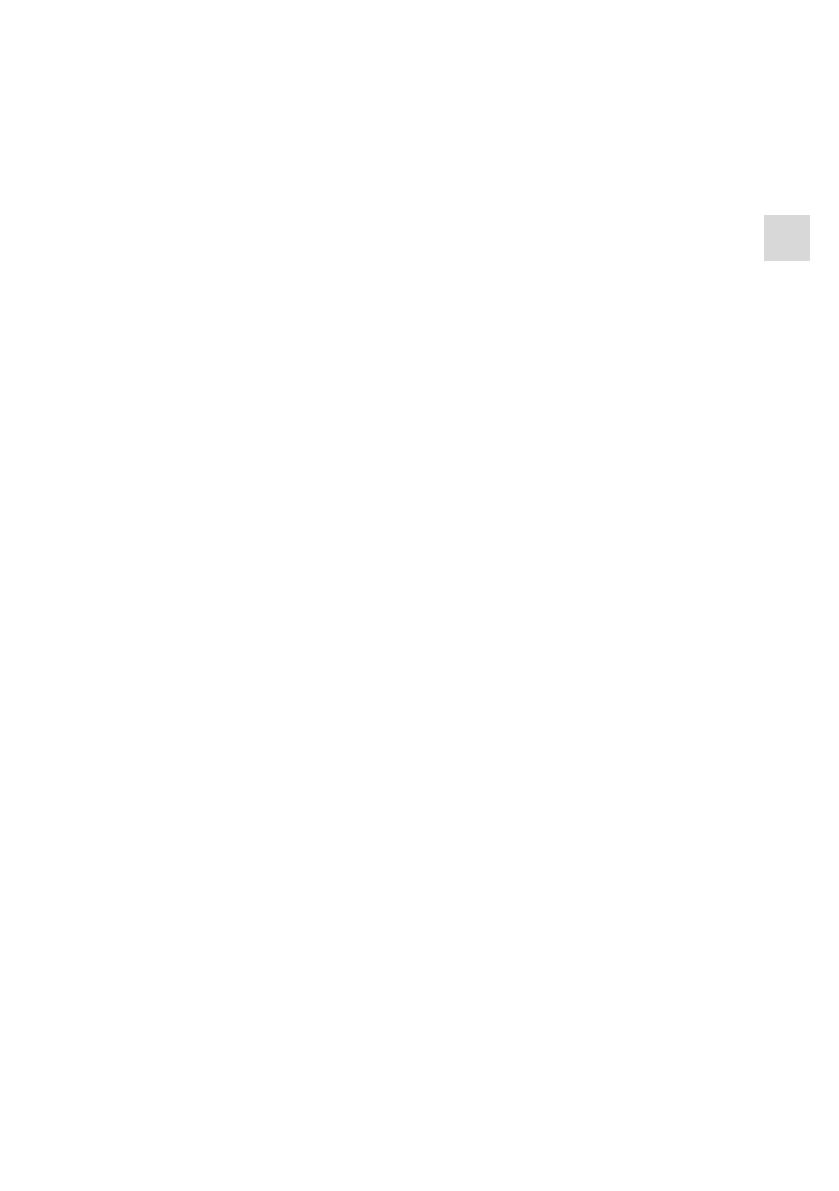
17/80
EN
9. ALARM CONDITIONS
GENERAL FUNCTION OF ALARM SYSTEMS
Gas alarm monitors the alarm conditions from the Pressure Watch. The display shows high or
low pressure for 1-6 gases.
See instruction for use for Gas alarm.
9.1.ALARM PROCEDURE
On signal of alarm condition, the appropriate visual indicator is appeared on the gas alarm.
The alarm condition should be recorded, and the necessary action taken, as detailed in the
sections below.
9.2.STATUS INDICATED BY ALARM
9.2.1.ABNORMAL POSITION OF VALVES
Abnormal positions of valves can be detected if there are position switches on valves. In this
case should be the necessary action taken for safety operation and continuous gas supply.
9.2.2.HIGH SUPPLY PRESSURE
Check that the outlet pressure is as preferred. If not, fi x the problem with gas source or use
diff erent source.
9.2.3.LOW SUPPLY PRESSURE
Check that the outlet pressure is as preferred. If not, fi x the problem with gas source or use
diff erent source.
9.2.4.SLIDE DOOR ARE OPEN
Open position of door can be detected if there are position switch on door. In this case should
be the necessary action taken for safety operation and continuous gas supply.
10. ROUTINE MAINTENANCE INSTRUCTION
Service shall be carried out only by authorised person according to national standards.
Use only original components. Contact GCE for further information about repair procedures.
THE FOLLOWING ROUTINE CHECKS SHOULD BE MADE ON A WEEKLY BASIS:
• Check all valves for correct operation and leak test using a 0.5% teepol in water solution.
• Check pipe work for leaks using a 0.5% teepol in water solution.
• Check that all notices are in place, can be easily read and are not obstructed from view.
• Inspect the vicinity of cylinders for anything introduced since last inspection, which could
aff ect the continuing safe operation of the manifold.
GENERAL MAINTENANCE SHOULD BE UNDERTAKEN IN ACCORDANCE WITH A PLANNED
MAINTENANCE SCHEDULE, WHICH SHOULD INCLUDE THE FOLLOWING ITEMS:
• Leak test all joints using a 0.5% teepol in water solution.
• Examine mounting frames and cylinder securing chains for damage deterioration and security
of attachment. programme.
• Valves to be used in normal or emergency operation are accessible and easy to operate.
Valves at service point’s outlets and purge valves should be checked for gas tightness.
• No item of equipment is overdue for any periodic inspection/test which may be applicable.
• The setting and operation of regulators is satisfactory.
• The necessary safety devices and instruments are fi tted, are of the correct type and do not
show signs of deterioration or unauthorised interference.
• The equipment downstream of the outlet point is suitable for further service.
• Check connecting nuts and seating faces are undamaged.
• Check o-rings are undamaged.
• Check gauges operate smoothly and zero correctly.
• Check isolating valves for closure tightness and gland leakage.
• The gas manifold room must always remain thoroughly clean. Materials other than those
required for operating the manifold must not be stored in the room.