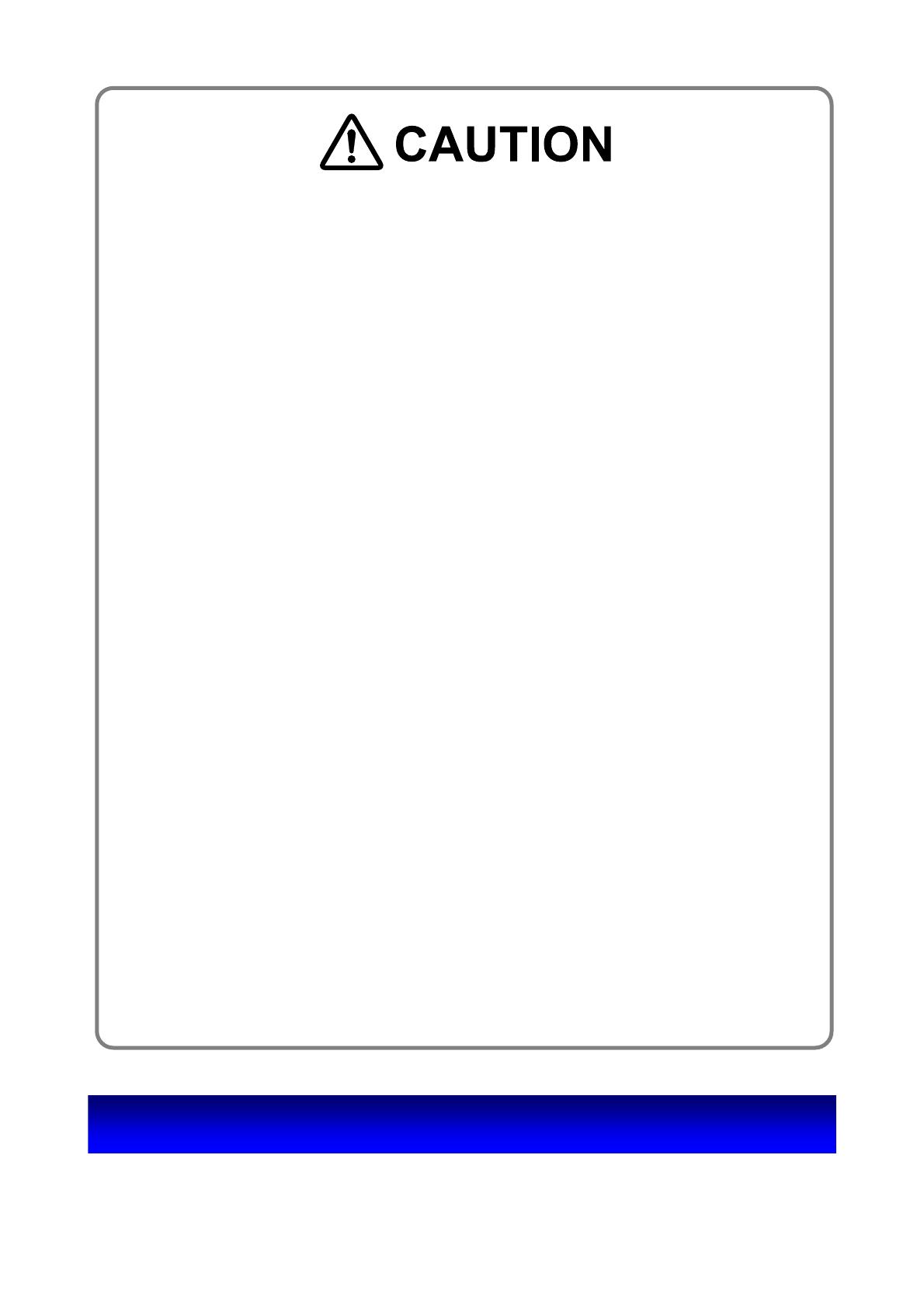
IMR02E20-E2
i-2
● This product is intended for use with industrial machines, test and measuring equipment.
(It is not designed for use with medical equipment and nuclear energy plant.)
● This is a Class A instrument. In a domestic environment, this instrument may cause radio
interference, in which case the user may be required to take additional measures.
● This instrument is protected from electric shock by reinforced insulation. Provide reinforced
insulation between the wire for the input signal and the wires for instrument power supply,
source of power and loads.
● Be sure to provide an appropriate surge control circuit respectively for the following:
- If input/output or signal lines within the building are longer than 30 meters.
- If input/output or signal lines leave the building, regardless the length.
● This instrument is designed for installation in an enclosed instrumentation panel. All
high-voltage connections such as power supply terminals must be enclosed in the
instrumentation panel to avoid electric shock to operating personnel.
● All precautions described in this manual should be taken to avoid damage to the instrument or
equipment.
● If the equipment is used in a manner not specified by the manufacturer, the protection provided
by the equipment may be impaired.
● All wiring must be in accordance with local codes and regulations.
● To prevent instrument damage as a result of failure, protect the power line and the input/output
lines from high currents with a suitable overcurrent protection device with adequate breaking
capacity such as a fuse, circuit breaker, etc.
● A malfunction in this product may occasionally make control operations impossible or prevent
alarm outputs, resulting in a possible hazard. Take appropriate measures in the end use to
prevent hazards in the event of malfunction.
● Prevent metal fragments or lead wire scraps from falling inside instrument case to avoid electric
shock, fire or malfunction.
● Tighten each terminal screw to the specified torque found in the manual to avoid electric shock,
fire or malfunction.
● For proper operation of this instrument, provide adequate ventilation for heat dissipation.
● Do not connect wires to unused terminals as this will interfere with proper operation of the
instrument.
● Turn off the power supply before cleaning the instrument.
● Do not use a volatile solvent such as paint thinner to clean the instrument. Deformation or
discoloration may occur. Use a soft, dry cloth to remove stains from the instrument.
● Do not connect modular connectors to telephone line.
When disposing of each part used for this instrument, always follows the procedure for
disposing of industrial wastes stipulated by the respective local community.
For Proper Disposal