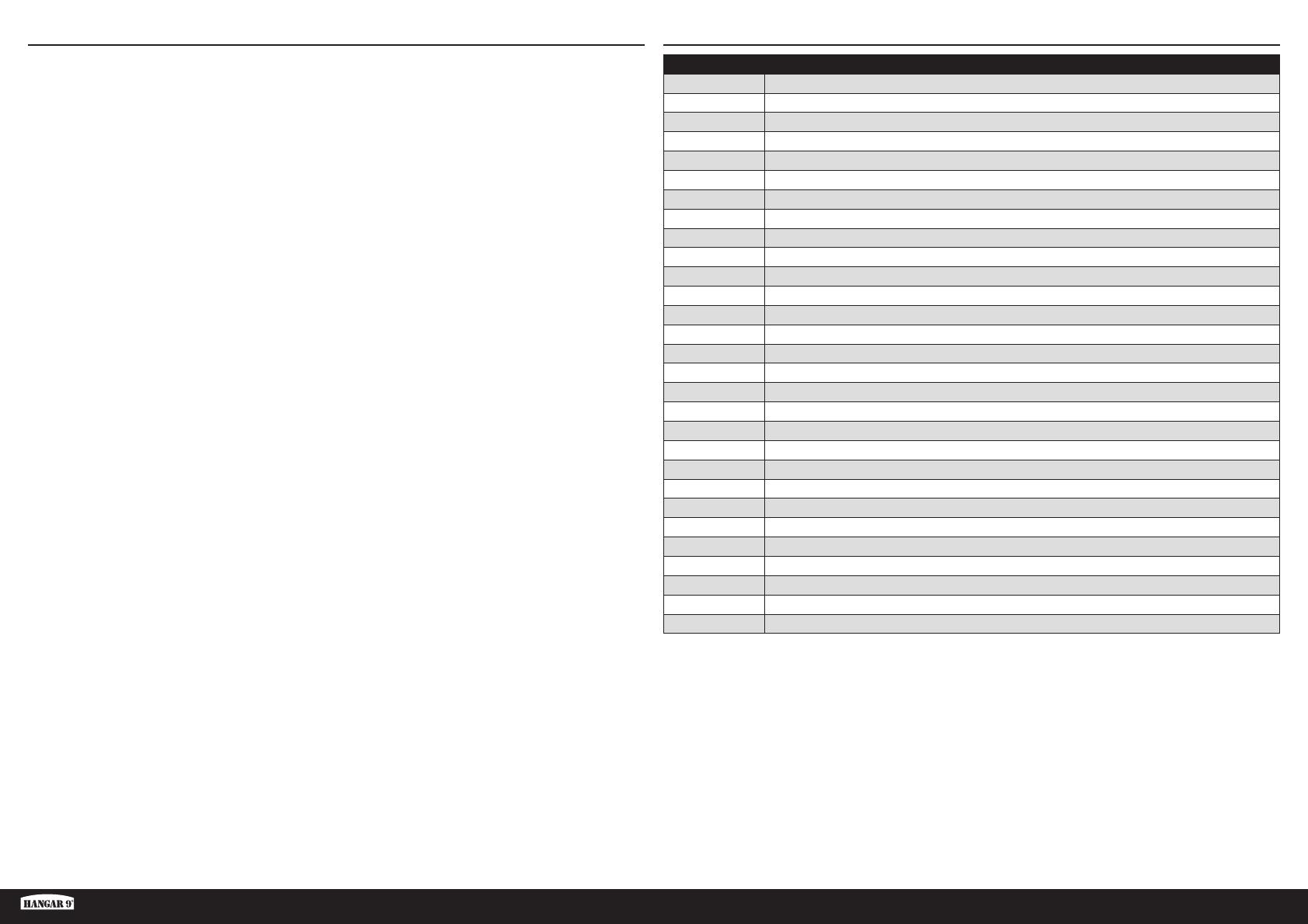
3 EN
OV-10 Bronco 30cc
Part # Description
HAN467001 Nacelle/Boom; Left-Hand
HAN467002 Nacelle/Boom; Right-Hand
HAN467003 Fuselage
HAN467004 Wing Panel; Left-Hand
HAN467005 Wing Panel; Right-Hand
HAN467006 Wing Panel; Center
HAN467007 Stabilizer with Elevator
HAN467008 Rudders (2)
HAN467009 Cowlings (2)
HAN467010 Cockpit Hatch
HAN467011 Canopy
HAN467012 Pilot Figure
HAN467013 Pushrod Set
HAN467014 Hardware Set
HAN467015 Wheels; (3)
HAN467016 Landing Gear Set
HAN467017 Retract Set; Mains
HAN467018 Retract Unit; Nose
HAN467019 Landing Gear Controller
HAN467020 Retract Motor
HAN467021 Landing Gear Strut Set
HAN467022 Wing Tubes
HAN467023 EP Motor Mounts
HAN467024 Scale Parts
HAN467025 Fuselage Pods/Parts
HAN467026 Missiles and Pylons
HAN467027 Gear Door Set
HAN467028 Painted Spinners (2)
HAN467029 Decal Set
REPLACEMENT PARTS
TABLE OF CONTENTS
Notice ......................................................................................................................................................................2
Meaning of Special Language ..................................................................................................................................2
Safety Warnings and Precautions .............................................................................................................................2
Safe Operating Recommendations ...........................................................................................................................2
Before Starting Assembly .........................................................................................................................................2
FAA Information .......................................................................................................................................................2
Replacement Parts ...................................................................................................................................................3
Required for Completion ..........................................................................................................................................4
Required for Completion - EP ...................................................................................................................................4
Required for Completion - Gas .................................................................................................................................4
Optional Parts for Retract Doors ...............................................................................................................................4
Optional Parts ..........................................................................................................................................................4
Required Adhesives .................................................................................................................................................4
Tools Required .........................................................................................................................................................5
Printed Covering Notes ............................................................................................................................................5
Building Precautions ................................................................................................................................................5
Transportation and Storage ......................................................................................................................................5
Checking Blind Nuts.................................................................................................................................................5
Hinging the Stabilizer and Elevator ...........................................................................................................................6
Building Considerations ...........................................................................................................................................6
Stabilizer Servo Installation ......................................................................................................................................8
Aileron and Aileron Servo Installation .....................................................................................................................10
Flap and Flap Servo Installation .............................................................................................................................12
Center Section Servo Leads ...................................................................................................................................14
Rudder and Rudder Servo Installation ....................................................................................................................14
Optional Retract Door Installation ...........................................................................................................................16
Main Gear Retract Installation ................................................................................................................................17
Nose Gear Retract Installation ................................................................................................................................19
Electric Motor Installation .......................................................................................................................................20
Gas Engine Installation ...........................................................................................................................................21
Fuel Tank Installation .............................................................................................................................................23
Gas Engine Spinner and Propeller Preparation .......................................................................................................24
Cowling Installation................................................................................................................................................25
Radio Installation ...................................................................................................................................................27
Accessory Installation ............................................................................................................................................29
Final Assembly .......................................................................................................................................................32
Center of Gravity ....................................................................................................................................................32
Control Throws ......................................................................................................................................................33
Mixing ...................................................................................................................................................................33
Prefl ight Checklist ..................................................................................................................................................33
Daily Flight Checks ................................................................................................................................................33
Limited Warranty ...................................................................................................................................................34
Warranty and Service Contact Information .............................................................................................................35
Instructions for Disposal of WEEE by Users in the European Union ..........................................................................35
Academy of Model Aeronautics National Model Aircraft Safety Code .......................................................................35