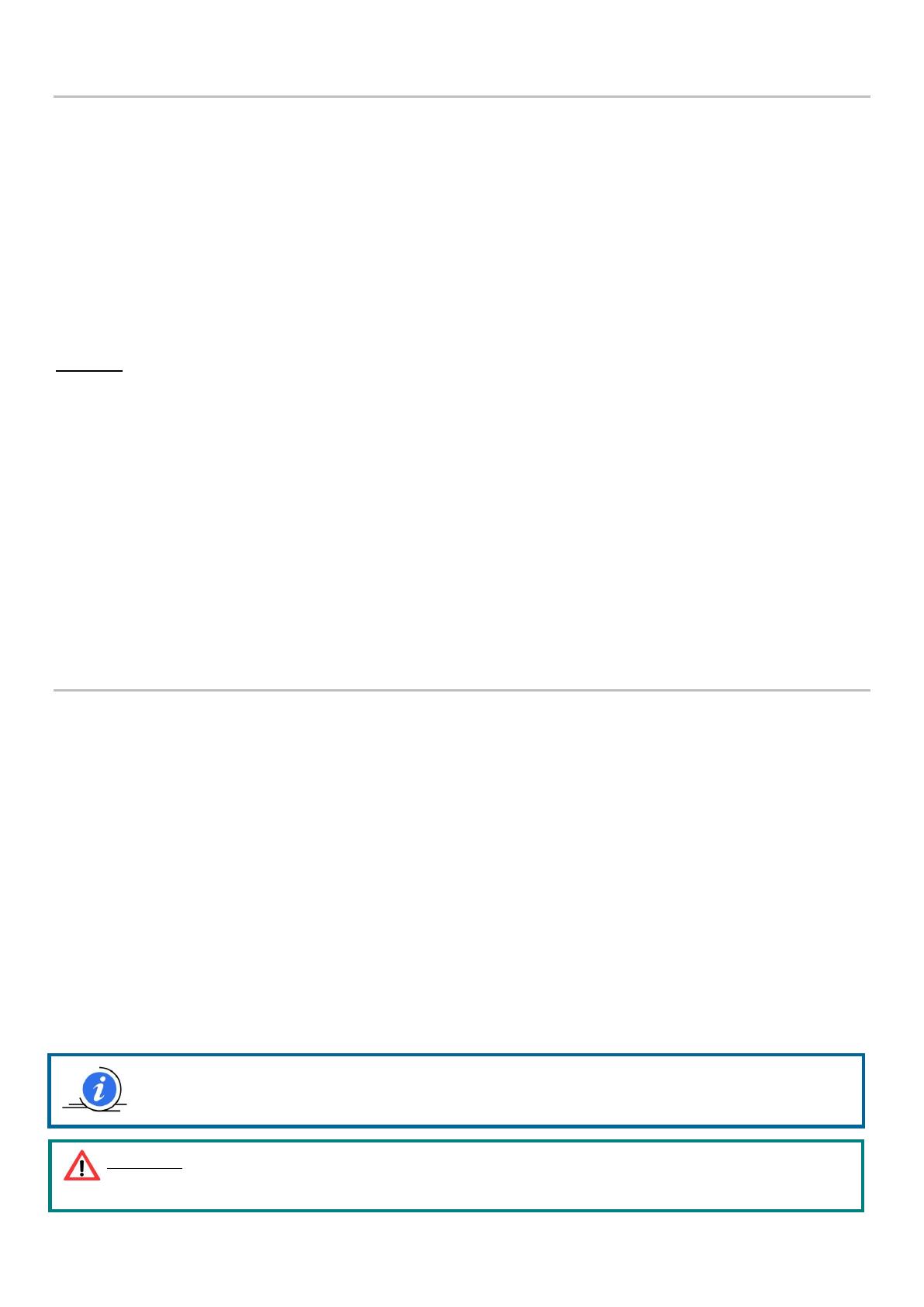
6
6. UNPACKING AND INSTALLATION
6.1 UNPACKING
Once a suitable location has been found to install the unit remove the machine from the packaging. Check the device has not
been damaged during transportation or storage. No particular disposal procedures are necessary, as packaging materials are not
dangerous or polluting. Refer to the local regulations for disposal.
6.2 INSTALLATION
Unit can be installed only by a trained staff familiar with hazardous area equipment.
Not use the flow metering device submerged in fluids or in corrosive environments.
Use protective gloves and safety glasses as provided in data sheet of the lubricating oil.
DO NOT use lubricants that are incompatible with NBR rubber gaskets, in case of doubt consult a Dropsa engineering.
Do not ignore dangers to health and observe all normal necessary safety precautions.
WARNING!: All components must be grounded. This applies both to the electrical components and control devices. To do this,
make sure that the grounding wire is properly connected. For safety reasons, the earth conductor should be about 100 mm
longer than the phase conductors. In case of accidental disconnection of the cable, the protective earth terminal will be the last
to come off.
Installation Requirements
To install the flow meter you should follow these steps:
Verify classification of the hazardous area;
flow metering device installation must be in an area where it is protected from accidental shocks;
It is not suitable to be installed outdoors, unless protection against rain and water splashes is applied;
Avoid possible salt spray that could compromise the corrosion resistance of the mechanical parts;
ATTENTION! Inductive sensor is EEx ia type: It can work in Ex hazardous area only if it is interfaced with an
INTRINSICALLY SAFE ISOLATED BARRIER, to be installed by customer and not included with the sensor.
7. INSTRUCTIONS FOR USE
7.1 INSTRUCTION FOR START UP
Before starting the first time make following checks:
1. Check the integrity of all parts;
2. Make sure that you use a suitable lubricant;
3. Verify that the environment temperature is within the working range;
4. Make sure that the electrical connection of the inductive sensor is properly executed;
5. Ensure correct procedures for venting environment.
7.2 INSTRUCTIONS FOR USE
1. Program the calibration curve of the sensor for the pressure range (0-400 bar) into your control system;
2. Check that there is a regular reading of the inductive sensor once the system is purged;
3. Make sure that during operation there are no leaks and monitor that there is regular output from the inductive sensor
(flashing light).
7.3 INSTRUCTIONS FOR EMERGENCY SHUTDOWN
ATTENTION: In case of emergency shutdown of lubrication system, the flow meter will indicate a loss of impulses due to a flow failure
across the device. The host machine’s control system should monitor this alarm condition and determine if a shutdown of the machines
is necessary in order to avoid possible damage (seizures).
Note: The Flow sensor is not equipped with command electrical device. All operating logic must be
implementing by the customer.