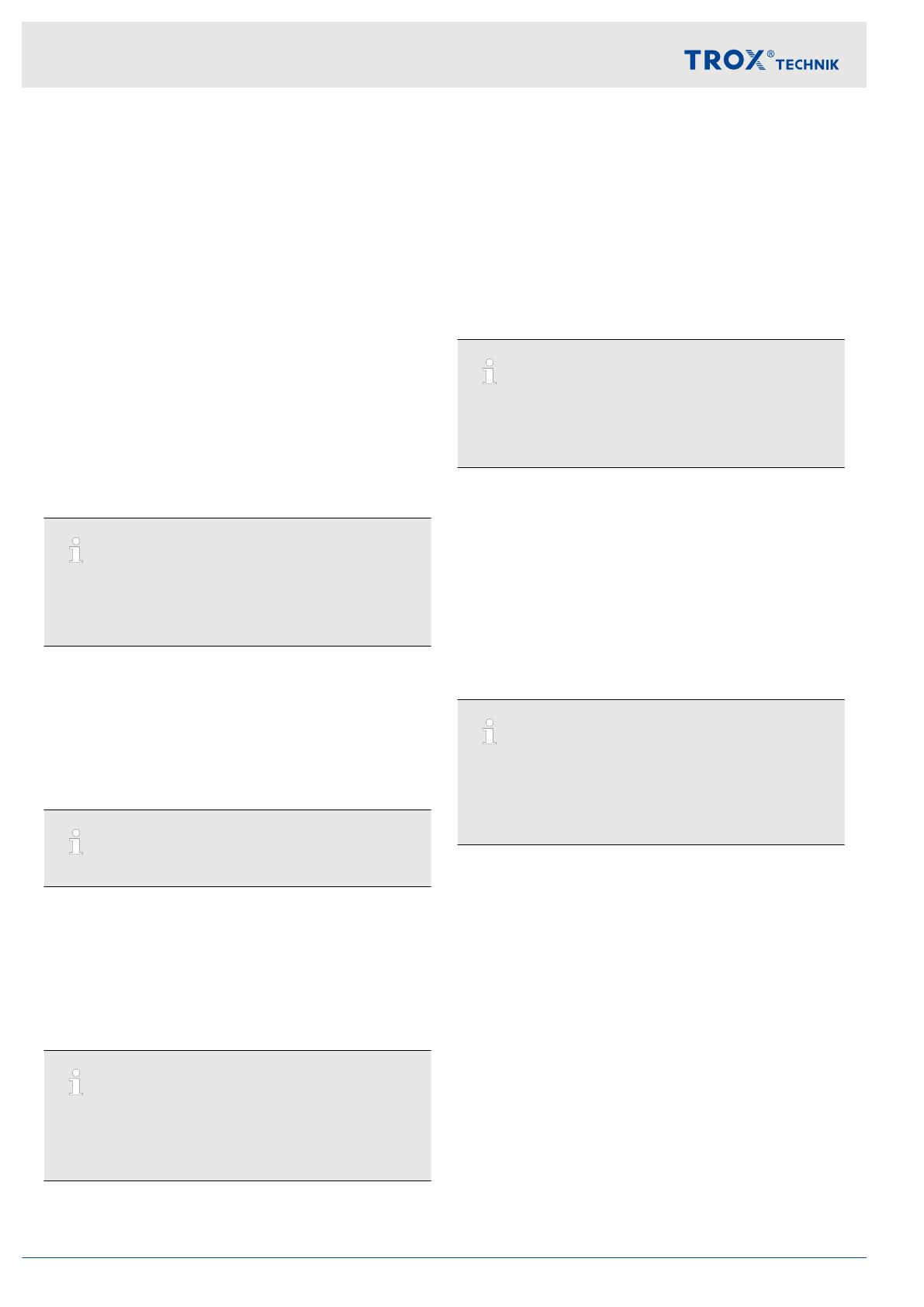
The specified operating modes and overrides can be set
using the optional real-time clock and the central BMS.
In addition, the Occupied and Unoccupied operating
modes as well as the Boost and Exercise overrides can
be activated from the control panel.
Various comfort temperature ranges can be defined for
the operating modes Occupied and Unoccupied. You
can define daily schedules and enter a start time for
each operating mode. Using the optional real time clock
(RTC) allows for defining 10 switching points per day. If
no RTC is used, operating modes must be changed by
the central BMS or on the control panel. The comfort
temperature range for the Occupied mode can be modi-
fied on the control panel and by the central BMS.
Standby operating mode
Standby is selected if the room is not occupied and the
ventilation units are not used to maintain the tempera-
ture, e.g. at night.
Recommended:
Standby is used exclusively to protect the device. It
should be selected for periods of prolonged down-
time, e.g. vacation periods, as long as the building
protection is ensured by other heat sources.
Occupied operating mode
The Occupied mode is used for occupied rooms.
The following parameters can be set:
Comfort temperature range for the Occupied mode
Supply air temperature limits for heating/cooling
Recommended
All-day use (e.g. 7am to 5 pm)
Unoccupied operating mode
The Unoccupied mode is used for unoccupied rooms.
The following parameters can be set:
Comfort temperature range for Unoccupied mode
Supply air temperature limits for heating/cooling
Unoccupied
–This operating mode is used to protect the
building; it is required for night purge.
–Air quality control is not possible with this oper-
ating mode.
Boost operating mode override
Boost can be selected to quickly ventilate a room, e.g.
during break times. The device ensures supply air/
extract air operation to improve the indoor air quality.
Afterwards, the device returns to the Occupied oper-
ating mode.
The following parameters can be set:
Fan setting (default: stage 4)
Duration (default: 15 mins)
Boost
Boost mode can be enabled using the control panel
or central BMS. The same setpoint values that are
used for Occupied mode are used for the comfort
temperature range and supply air temperature limits.
Exercise operating mode override
Exercise can be selected if acoustically optimised oper-
ation is required. The device conveys a slightly reduced
volume flow rate in supply air/extract air operation to
improve the indoor air quality. Afterwards, the device
returns to the Occupied operating mode.
The following parameters can be set:
Fan setting (default: stage 2)
Duration (default: 60 mins)
Exercise
Exercise mode can be enabled using the room con-
trol panel or the central BMS The same setpoint
values that are used for Occupied mode are used for
the comfort temperature range and supply air tem-
perature limits.
Nigh purge operating mode override
With the Night purge function, the room is passively
cooled with outdoor air. The minimum supply air temper-
ature corresponds to the supply air temperature limit for
heating in Unoccupied mode of -2K. The fans are con-
trolled in the configured stage for night ventilation. The
max. fan stage for Unoccupied operating mode is
ignored for the duration of night ventilation.
The following conditions must be simultaneously ful-
filled:
Night purge is activated
The current month is in the range Start – End –
Month (default: May – September)
Activated by RTC, central BMS or DI
Outdoor air temperature > minimum outdoor air tem-
perature for Night purge (default = 12 °C)
Outdoor air temperature < as a setpoint value for
cooling in the Occupied operating mode
Control of the ventilation unit
FSL-CONTROL III controller > Functional description
Single room control system FSL-CONTROL III20