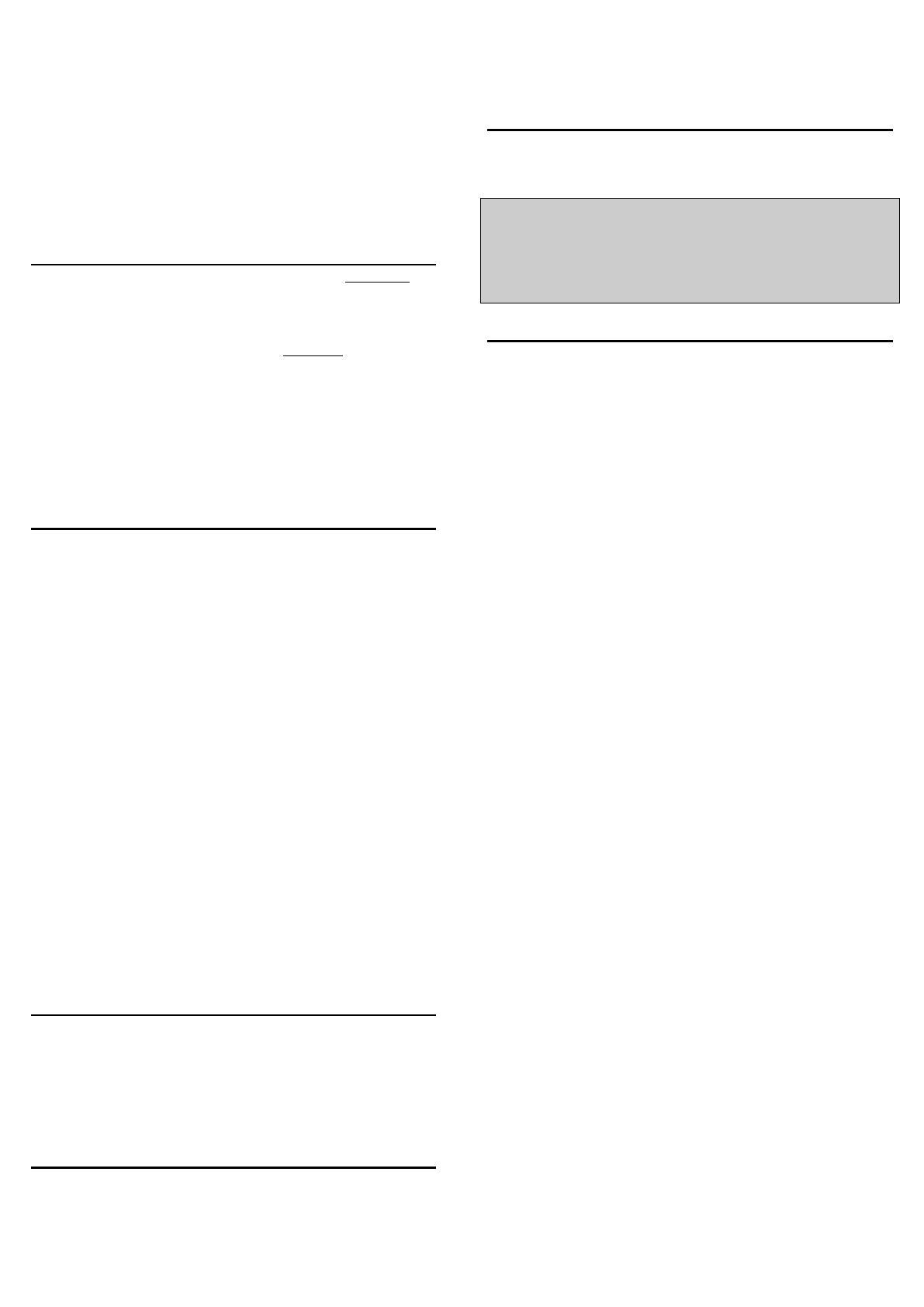
• If the belt has been subject to significant paint
overspray, it must not be used.
• Check connectors for correct operation ensuring
there is no tendency for them to stick or jam.
• Adjusters and connectors must be free from rust,
excessive wear, distortion or cracks.
If during the pre-use check the belt is found to be or
believed to be faulty DO NOT use it. Remove from site to
ensure it cannot be used by anyone else.
Textile products including webbing and rope
be
marked using ink or paint. Marker pens and paint will
contaminate textile fibres leading to potential damage from
material stiffening or even chemical attack.
Plastic or Metal casings of components
be marked by
stamping, etching or engraving. These processes may weaken
the material or damage protective coatings.
advise that if additional identification is required a tagging
system (label or electronic) should be used that does not
interfere in any way with the operation of equipment or
devices. Contact
or your supplier for advice on additional
labelling.
Cleaning, Maintenance and Storage
Keep the
P&P Work Positioning Belt
clean and dry. Remove
excess moisture with a clean cloth then allow drying naturally
in a warm room away from direct heat.
You may clean this belt using water but avoid getting
soap/detergent into buckles. First rinse in clean cold water – if
still soiled; wash in clean warm water (40ºC max) using a mild
detergent if necessary. Thoroughly rinse in clean cold water
and dry as described above.
Avoid contact with any chemical, which might affect the
performance of this belt, e.g these include all acids and strong
caustic substances (vehicle battery acid, bleach etc)
If subject to chemical attack, you must remove it from service
and check with the supplier or
for advice on the possible
consequence of chemical degradation.
After any necessary cleaning, dry completely then store in a
cool dry place, which will protect it from extreme humidity and
direct heat.
Care should be taken to protect the belt against risks such as
those detailed under Service Life. A simple effective way is to
transport the belt in a suitable bag or container which prevents
abrasion.
The
has a maximum life span of 10 years from date of
manufacture, provided it is correctly stored and maintained.
However, if the belt fails any inspection it MUST be destroyed.
See the Statement of Obsolescence within this manual.
This User Manual is for English speaking countries only. If you
require this manual in a different language, please Contact
.
When this item is sold on, this manual must accompany it and
be supplied in the language of the destination country.
The Product Code, Serial number and Date of Manufacture of the
P&P Work Positioning Belt
should be entered on the back page of
this manual for future reference and inspection purposes.
Warning
This
P&P Work Positioning Belt
must be used by persons who are
medically fit to do so. If you have any medical condition, are
recovering from any medical condition or suffer from any physical or
mental disability you must seek professional medical advice before
using this
P&P Work Positioning Belt
.
Statement of Obsolescence
Due to the ingress of dirt and grit, chemical contamination, edge and
surface damage, ultraviolet light degradation, and wear and tear, Fall
Protection Equipment manufactured from synthetic fibres (webbing
and/or rope) is subject to a manufacturer’s statement of obsolescence,
which is a requirement of BS EN 365:2004 a European Product
Standard.
Any item of Fall Protection Equipment manufactured by
with
synthetic fibre components (webbing and/or rope) is subject to
maximum life span of 10 years from date of manufacture, provided
that the item has been correctly stored, maintained and subjected to
regular recorded inspections by a trained and competent person.
However, if the item fails any inspection, it MUST immediately be
withdrawn from service and destroyed.
An item of Fall Protection Equipment incorporating synthetic fibre
components (webbing and/or rope), manufactured by
from
January 2015, which has been subject to a lifetime recorded inspection
plan, may give a maximum life span of 10 years. The lifetime recorded
inspection plan must be continuous from date of first use and be
undertaken by a competent person appointed by the employer.
Competent persons must be trained in the use and inspection of the
equipment. The lifetime inspection plan must include as a minimum
requirement, a pre use check and 6 monthly recorded inspections.
The frequency of inspections should be determined by risk
assessment, use and environmental conditions.
Reference should also be made to the British Standard BS 8437:2005 –
‘The code of practice selection, use and maintenance of personal fall
protection systems and equipment for use in the workplace’ - clause
13.2 Lifespan, which states:
‘Some equipment is given a life span or obsolescence date by the
manufacturer. Equipment that has reached such a limit, which has not
already been rejected for other reasons, should be withdrawn from
service and not used again, unless or until confirmed by a competent
person, in writing, that it is acceptable to do so.’
It should be noted that inspections carried out by a trained and
competent person are only visual and tactile observations of the
condition of the product; they are not testing the residual strength of
the equipment. All synthetic fibres deteriorate slowly with age
regardless of use and as a result,
strongly advises all users of Fall
Protection Equipment to follow the manufacturer's statement of
obsolescence.
For further advice on this statement, as well as training in the use and
inspection of Fall Protection Equipment, please contact