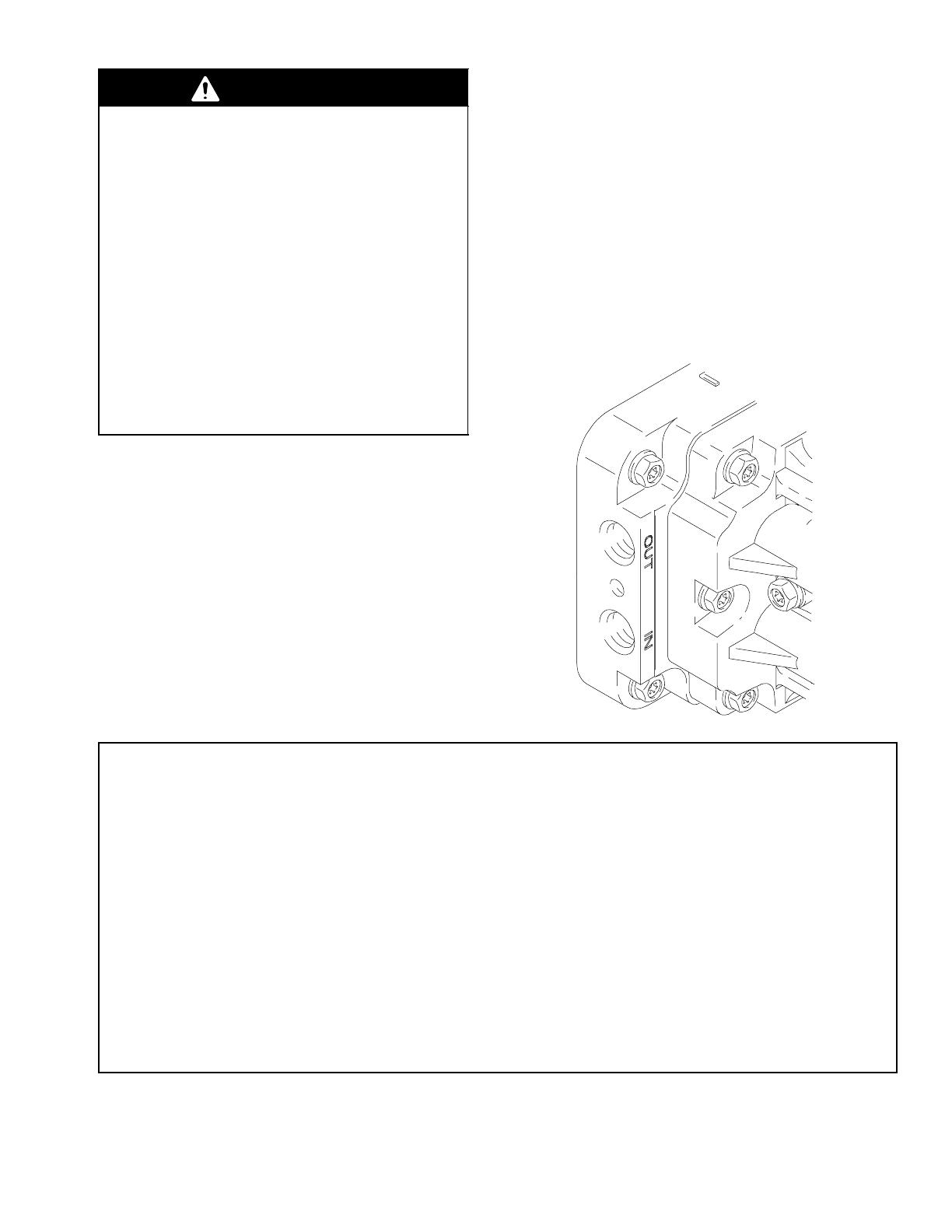
5
Air Lines
WARNING
Bleed-Type Master Air Valve and Fluid Drain
Valve
A bleed-type master air valve and a fluid drain valve
are required on your system.
The bleed-type master air valve relieves air trapped
between itself and the pump. Trapped air can cause
the pump to cycle unexpectedly, which could result in
serious bodily injury, including splashing in the eyes,
injury from moving parts, or contamination from
hazardous fluids.
The fluid drain valve reduces the risk of serious
bodily injury, including splashing in the eyes or on the
skin, or contamination from hazardous fluids. Install
the fluid drain valve close to the pump’s fluid outlet to
relieve pressure in the hose if the hose becomes
plugged.
1. Mount the air line accessories on the wall or on a
bracket. Be sure the air line supplying the accessories
is grounded.
a. The pump speed can be controlled in one of two
ways: To control it on the air side, install an air
regulator (Order Graymills Part No. FRL–2). To
control it on the fluid side, install a fluid valve
near the outlet.
b. Install a bleed-type master air valve downstream
from the air regulator, and use it to relieve trapped
air. See the Bleed-Type Master Air Valve and
Fluid Drain Valve warning on page 5. Locate
another bleed-type master air valve upstream from
all air line accessories, and use it to isolate the
accessories during cleaning and repair.
c. The air line filter removes harmful dirt and mois-
ture from the compressed air supply.
2. Install a flexible air hose between the accessories and
the pump air inlet. Screw the air line fitting into the
air inlet.
3. Do not restrict the exhaust port. Excessive exhaust
restriction can cause erratic pump operation.
Fluid Lines
Fig. 1. On each end of the fluid manifold are a fluid IN port
and a fluid OUT port. NOTE: Make sure the fluid OUT
port on the fluid manifold is mounted up, Fig. 1. This
will assure proper pump priming. Fluid-in and fluid-out
lines can be connected on the same end, or opposite ends of
the manifold. Plug ports that are not used (plugs provided).
Figure 1
06179A
TECHNICAL DATA
Maximum fluid working pressure 100 psi (0.7 MPa, 7 bar)
Maximum / minimum air pressure 100 psi / 20 psi
(0.7 MPa, 7 bar)/(0.14 MPa, 1.4 bar)
Maximum fluid flow 5.0 gpm (18.9 lpm)
Maximum pump speed 320 (dry) cycles per minute
250 (wet) cycles per minute
Volume per stroke* 0.006 gal (23cc)
Volume per cycle* 0.012 gal (46 cc)
Maximum suction lift dry 8 to 10 ft (25 to 3 m)
Maximum size pumpable solids 0.06 in. (1.5mm)
Maximum operating temperature 180_ F (82_ C)
Maximum air consumption 9.0 scfm, (0.252 m 3 / min.)
Air inlet size** 1/4 npt (f) 1/4 bsp (f)
Fluid inlet size** 1/4 npt(f) / 1/4 bsp(f)
Fluid outlet size** 1/4 npt(f) / 1/4bsp (f)
Air exhaust port size** 1/4 npt (f) / 1/4 bsp (f)
Weight (Polypropylene pump) 2.0 lb (0.9 kg)
Wetted parts (housing, diaphragms, check valves) Glass–filled
polypropylene, Teflon, polypropylene.
Sound power level (pressure) (per ANSI STD S12.1)
at 100 psi (0.7 MPa, 7 bar) 75.5 dBa
at 70 psi (0.49 MPa, 4.9 bar) 72.0 dBa
at 40 psi (0.28 MPa, 2.8 bar) 68.2 dBa
Sound power level (intensity) (per ANSI STD S12.1)
at 100 psi (0.7 MPa, 7 bar) 84.5 dBa
at 70 psi (0.49 MPa, 4.9 bar) 81.1 dBa
at 40 psi (0.28 MPa, 2.8 bar) 76.6 dBa
* Volume per cycle may vary based on suction condition, dis-
charge head, air pressure, and fluid.
** Hybrid thread allows for either 1/4 npt or 1/4 bsp fitting.
Teflon is a registered trademark of the DuPont Company.