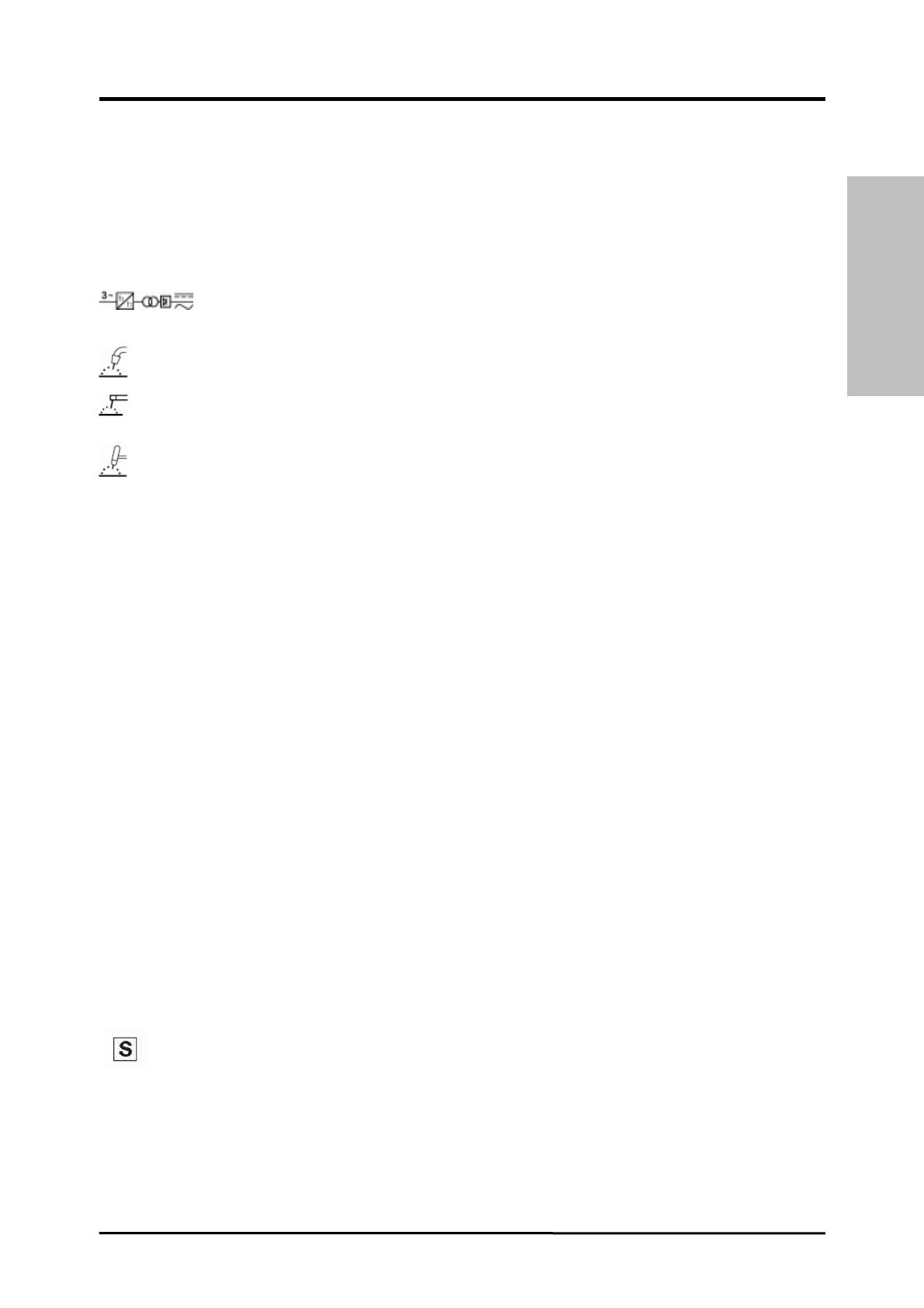
CEBORA S.p.A. 7
I
4.2 Dati tecnici.
Il Generatore è costruito secondo queste norme
internazionali:
IEC 60974-1 / IEC 60974-5 / IEC 60974-10 (CL . A);
IEC 61000-3-11 / IEC 61000-3-12 (vedi nota a fine
paragrafo).
N°. Numero di matricola da citare per
ogni richiesta relativa al Generatore.
Convertitore statico di frequenza
trifase
.
Trasformatore - raddrizzatore.
MIG Adatto per saldatura MIG/MAG.
MMA Adatto per saldatura con elettrodi
rivestiti.
TIG Adatto per saldatura TIG.
U0. Tensione a vuoto secondaria.
X. Fattore di servizio percentuale. Il
fattore di servizio esprime la
percentuale di 10 minuti in cui il
Generatore può lavorare ad una
determinata corrente senza
surriscaldarsi.
I2. Corrente di saldatura.
U2. Tensione secondaria con corrente I2.
U1. Tensione nominale di alimentazione.
3~ 50/60Hz Alimentazione trifase 50 / 60 Hz.
I
1
Max Corrente max. assorbita alla
corrispondente corrente I
2
e tensione
U
2
.
I
1
eff E’ il valore massimo della corrente
effettiva assorbita considerando il
fattore di servizio. Solitamente,
questo valore corrisponde alla
portata del fusibile (di tipo ritardato)
da utilizzare come protezione per l’
apparecchio.
IP23S Grado di protezione della carcassa.
Grado 3 come seconda cifra
significa che questo apparecchio può
essere immagazzinato, ma non
impiegato all’esterno durante le
precipitazioni, se non in condizione
protetta.
Idoneo a lavorare in ambienti con
rischio accresciuto.
NOTE: Questi Generatori sono idonei a lavorare
con grado di inquinamento 3 (vedi
IEC60664).
Sono conformi alla norma IEC 61000-3-
12 a condizione che l’impedenza
massima Zmax ammessa dell’impianto
sia inferiore o uguale a 0.090 (art. 316 e
317), 0.094 (art. 315) al punto di
interfaccia fra l’impianto dell’utilizzatore
e quello pubblico.
E’ responsabilità dell’installatore o
dell’utilizzatore dell’attrezzatura
garantire, consultando eventualmente
l’operatore della rete di distribuzione, che
i Generatori siano collegati a
un’alimentazione con impedenza
massima di sistema ammessa Zmax
inferiore o uguale a 0.090 (art. 316 e
317), 0.094 (art. 315).
4.3 Descrizione comandi e attacchi (fig. 4).
A Connettore. Connettore tipo DB9 (linea
RS232) utilizzata per aggiornare i programmi
del Sistema di Saldatura (Generatore, Carrello
Trainafilo e Pannello di Controllo).
B Connettore. Connettore tipo USB utilizzata
per aggiornare i programmi del Sistema di
Saldatura (Generatore, Carrello Trainafilo e
Pannello di Controllo).
C Presa. Collegare il connettore del cavo di
massa (potenziale del pezzo da saldare).
D Raccordo tubo gas. Non usato in MIG.
E Connettore. Collegare il connettore del cavo
dei servizi della prolunga (2) Generatore -
Carrello Trainafilo.
F Presa. Collegare il connettore del cavo di
potenza della prolunga (2) Generatore -
Carrello Trainafilo.
G Interruttore. Per inserimento del resistore di
terminazione sulla linea CANbus-2 (default =
OFF).
H Interruttore. Non usato (default = OFF).
I Connettore CANbus-2. Collegare il cavo (3)
per il collegamento Generatore – Interfaccia
Robot o Controllo Robot.
L Connettore CANbus-1. Collegare il cavo (1)
per il collegamento Generatore – Pannello di
Controllo.
M Interruttore. Interruttore generale del
Sistema di Saldatura (Generatore, Carrello
Trainafilo, Pannello di Controllo e Interfaccia
Robot) (esclusa la parte di gestione Robot).
N Cavo di alimentazione.
O Portafusibile. Fusibile inserito sulla
alimentazione del Gruppo di Raffreddamento.
P Presa per Gruppo Raffreddamento.
Collegare il cavo di alimentazione del Gruppo
di Raffreddamento GRV12.
Q Presa pressostato. Collegare il cavo del
pressostato del Gruppo di Raffreddamento
GRV12.
3.300.354 15-04-2013