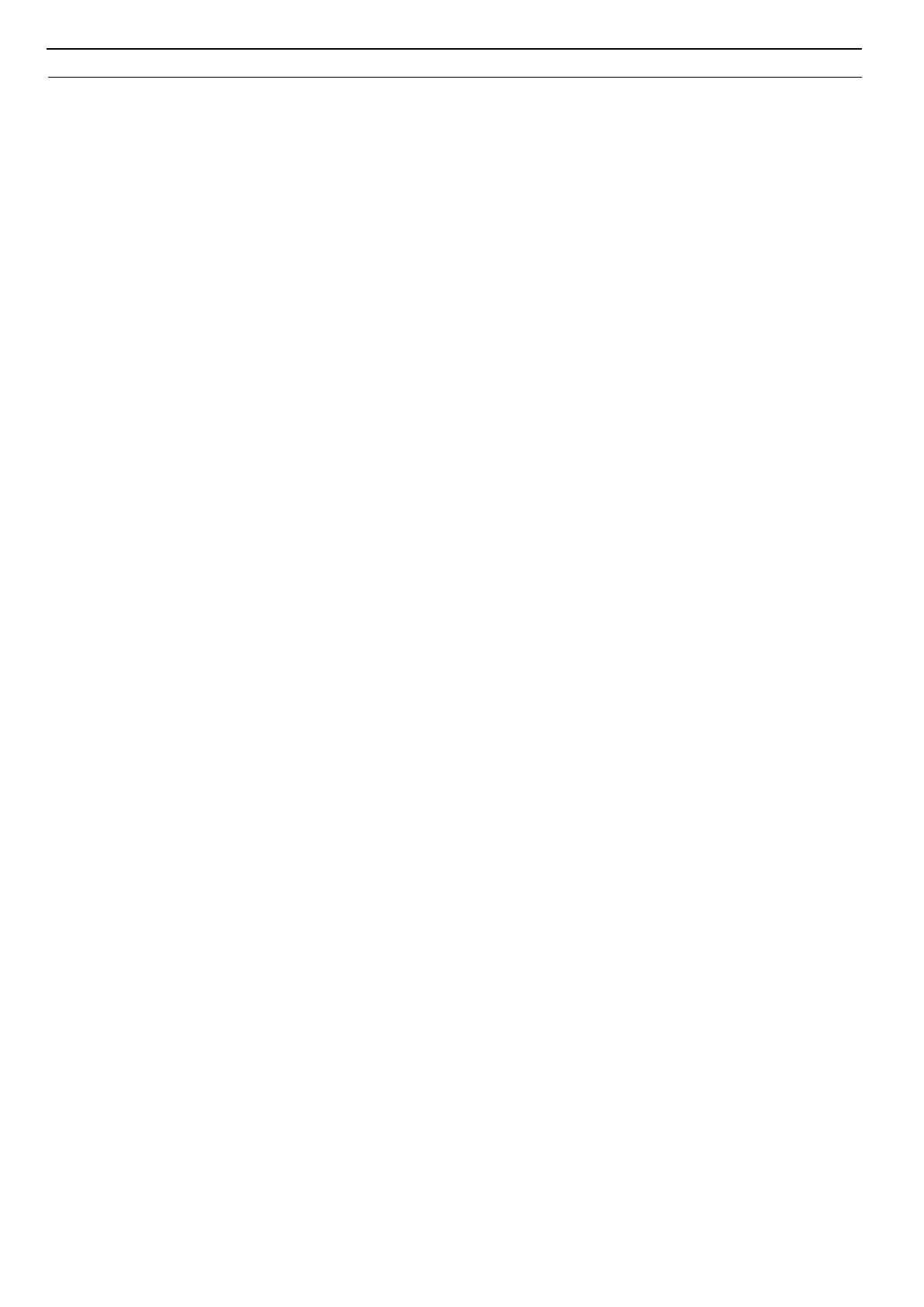
10 SOI/266-XC | 2600T Series Pressure transmitters 266 models
HARDWARE SETTINGS
HART
There are 6 dip switches located on this kind of secondary elec-
tronics (as indicated by the gure); they are used for settings
when integral display is not available.
Switch 1 and 2 allow the REPLACE MODE for sensor or secon-
dary electronics.
Switch 3 identies the external push buttons functionalities: Zero/
Span adjustments or PV Bias-Offset / PV Bias Reset.
Switch 4 and 5 are for Fail Low/Fail High selection.
Switch 6: not used.
The electronic label clearly explains how to perform all the pos-
sible selection, but please remember that all the operations with
the dip switches should be carried out when the transmitter is
powered off so as to upload new congurations at instrument
start-up.
Replace mode (switch 1 and 2)
Usually switches 1 and 2 are down in "0" position.
They are moved when a replace operation is required.
Switch 1 up in "1" position is required before power up the tran-
smitter, when user needs to replace the electronics or the sensor.
Switch 2 down in "0" position allows the replace of the secondary
electronics. It must be moved in this position before power up the
transmitter.
Switch 2 up in "1" position indicates that a new sensor has been
installed.
AFTER ANY REPLACE OPERATION IT IS RECOMMENDED TO
MOVE DOWN IN "0" POSITION THE RELEVANT SWITCHES.
Push buttons mode (switch 3)
Dip switch 3 is set at the factory on “0” position. This means that
the external push buttons perform the zero/span adjustments. If
the user puts this switch on “1” position, the zero push buttons will
modify the PV Bias-Offset and the span push button will reset the
PV Bias-Offset value.
Fail mode – Hardware switch (switch 4 and 5)
Should the user modify the factory-dened parameters for the fail
safe output condition in case of transmitter failure, it is necessary
to enable the modication by putting dip switch 4 on “1” position.
Consequently, it is necessary to choose whether the output has
to go Upscale or Downscale. Dip switch 5:
on “0” position the output is High
(above 20mA and more precisely 22mA)
on “1” position the output is Low
(below 4mA and more precisely 3,7mA)
FOUNDATION Fieldbus
There are 4 dip switches located on this kind of secondary elec-
tronics (as indicated by the gure); they are used for settings
when integral display is not available.
Switch 1 and 2 allow the REPLACE MODE for sensor or secon-
dary electronics.
Switch 3 identies the external push buttons functionalities: Zero/
Span adjustments or PV Bias-Offset / PV Bias Reset.
Switch 4 for performing the Simulation mode.
The electronic label clearly explains how to perform all the pos-
sible selection, but please remember that all the operations with
the dip switches should be carried out when the transmitter is
powered off so as to upload new congurations at instrument
start-up.
Replace mode (switch 1 and 2)
Usually switches 1 and 2 are down in "0" position.They are mo-
ved when a replace operation is required. Switch 1 up in "1" posi-
tion is required before power up the transmitter, when user needs to
replace the electronics or the sensor.
Switch 2 down in "0" position allows the replace of the secondary
electronics. It must be moved in this position before power up the
transmitter.
Switch 2 up in "1" position indicates that a new sensor has been
installed.
AFTER ANY REPLACE OPERATION IT IS RECOMMENDED TO
MOVE DOWN IN "0" POSITION THE RELEVANT SWITCHES.
Push buttons mode (switch 3)
Dip switch 3 is set at the factory on “0” position. This means that
the external push buttons perform the zero/span adjustments. If
the user puts this switch on “1” position, the zero push buttons will
modify the PV Bias-Offset and the span push button will reset the
PV Bias-Offset value.
Simulation mode (switch 4)
Dip switch 4 in “1” position enables the Simulation mode. This
feature is available in order to initialize all the parameters requi-
ring a well dened value, with the default values congruent to the
connected sensor type/model. This operation can be performed
before powering on the device. Many variables of the AI and TPB
are properly set with values strictly related to the connected tran-
sducer type.
PROFIBUS PA
There are 3 dip switches located on this kind of secondary elec-
tronics (as indicated by the gure); they are used for settings
when integral display is not available.
Switch 1 and 2 allow the REPLACE MODE for sensor or secon-
dary electronics.
Switch 3 identies the external push buttons functionalities: Zero/
Span adjustments or PV Bias-Offset / PV Bias Reset.
The electronic label clearly explains how to perform all the pos-
sible selection, but please remember that all the operations with
the dip switches should be carried out when the transmitter is
powered off so as to upload new congurations at instrument
start-up.
Replace mode (switch 1 and 2)
Usually switches 1 and 2 are down in "0" position.
They are moved when a replace operation is required.
Switch 1 up in "1" position is required before power up the tran-
smitter, when user needs to replace the electronics or the sensor.
Switch 2 down in "0" position allows the replace of the secondary
electronics. It must be moved in this position before power up the
transmitter.
Switch 2 up in "1" position indicates that a new sensor has been
installed.
AFTER ANY REPLACE OPERATION IT IS RECOMMENDED TO
MOVE DOWN IN "0" POSITION THE RELEVANT SWITCHES.
Push buttons mode (switch 3)
Dip switch 3 is set at the factory on “0” position. This means that
the external push buttons perform the zero/span adjustments. If
the user puts this switch on “1” position, the zero push buttons will
modify the PV Bias-Offset and the span push button will reset the
PV Bias-Offset value.