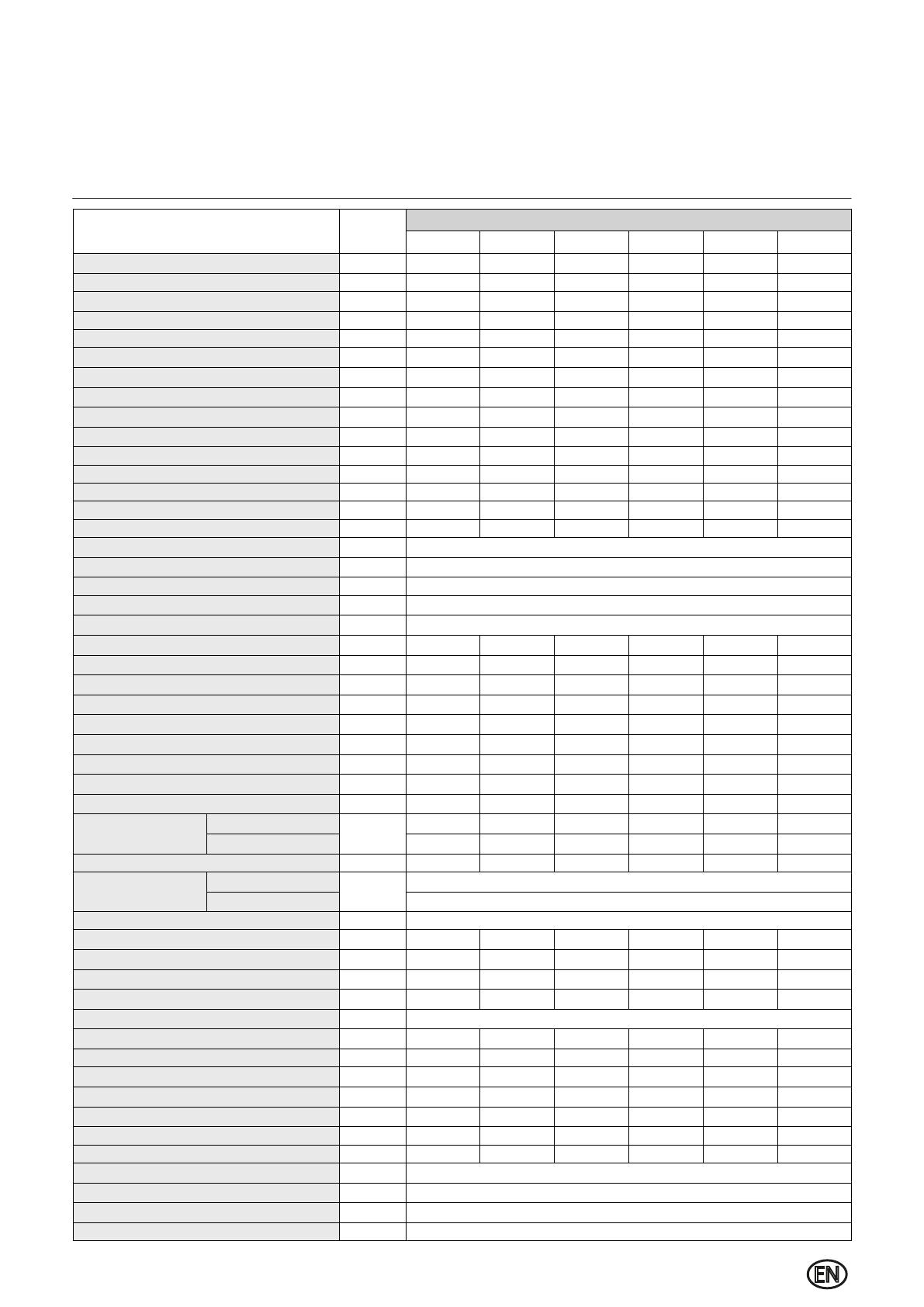
9
THISION L EVO
60 70 80 100 120 140
Nominal heat output at 80/60°C max/min
kW 56,5/15,5 65,5/15,6 75,3/19,4 92,9/18,7 111,9/22,5 130,4/26,2
Nominal heat output at 50/30°C max/min kW 60,4/17,2 70,0/17,2 79,7/21,2 98,9/20,6 118,5/24,8 137,8/28,9
Nominal heat output at 40/30°C max/min
kW 60,5/17,3 70,0/ 17,4 79,7/21,5 98,9/20,9 118,5/25,2 137,8/29,3
Nominal heat input Hi max/min kW 57,9/16,0 66,8/16,0 76,8/19,8 95,2/19,0 114,3/22,9 133,3/26,7
Modulaon rao - 3,6 4,2 3,9 5,0 5,0 5,0
Eciency at 80/60°C max/min
% 97,6/97,0 98,0/97,5 98,0/97,9 97,6/98,3 97,9/ 98,3 97,8/ 98,3
Eciency at 50/30°C max/min
% 104,4/107,4 104,8/107,3 103,8/107,2 103,9/108,5 103,7/108,4 103,4/108,3
Eciency at 40/30°C max/min
% 104,5/108,3 104,8/108,5 103,8/108,6 103,9/110,0 103,7/109,9 103,4/109,8
Eciency at 36/30°C load 30%
% 107,2 107,2 107,1 107,8 107,9 107,6
RAL 40/30 average
% 108,7 109,1 109,4 109,4 109,1 108,7
Heat Loss (Pstby) W 81,0 81,0 81,0 92,7 92,7 92,7
Max. condensate ow l/h 3,6 4,4 4,3 5,4 6,4 7,1
Gas consumpon G20 max/min (10,9 kWh/m
3
)
m
3
/h 5,3/1,5 6,1/1,5 7,0/1,8 8,7/1,7 10,5/2,1 12,2/2,4
Gas consumpon G25 max/min (8,34 kWh/m
3
)
m
3
/h 6,9/1,9 8,0/1,9 9,2/2,4 11,4/2,3 13,7/2,7 16,0/3,2
Gas consumpon G31 max/min (12,8 kWh/kg)
kg/h 4,5/1,3 5,2/1,3 6,0/1,5 7,4/1,5 8,9/1,8 10,4/2,1
Gas pressure G20
mbar 20
Gas pressure G25
mbar 25
Gas pressure G31 mbar 30/50
Maximum gas pressure
mbar 50
Max. temperature ue gas (high limit)
°C 90
Flue gas temperature at 80/60°C max/min
°C 59/57 60/57 61/58 60/56 63/56 66/57
Flue gas temperature at 50/30°C max/min
°C 43/35 44/34 45/33 44/33 46/33 48/33
Flue gas temperature at 40/30°C max/min
°C 42/33 44/33 44/33 43/32 45/32 47/32
Flue gas temperature at 36/30°C load 30%
°C 34 35 35 33 34 35
Flue gas quanty max/min
m
3
/h 83/22 98/22 113/27 139/27 168/33 202/38
CO level at 80/60 °C max/min
ppm 75/11 92/11 87/7 67/5 82/4 62/7
CO level at 80/60 °C max/min
mg/kWh 80/11 99/11 94/7 72/5 88/5 67/7
CO year emission EN15502
ppm 35,79 43,76 51,73 41,53 40,76 39,99
CO year emission EN15502
mg/kWh 38,44 47,00 55,56 44,60 43,78 42,95
CO
2
level G20-G25
Max. load
%
8,5 (+0 -0,2) 8,4 (+0 -0,2) 8,4 (+0 -0,2) 8,4 (+0 -0,2) 8,4 (+0 -0,2) 8,2 (+0 -0,2)
Min. load
9,0 (+0 -0,2) 9,0 (+0 -0,2) 9,0 (+0 -0,2) 8,5 (+0 -0,2) 8,5 (+0 -0,2) 8,5 (+0 -0,2)
Restricon ΔCO2 max.load - min. load (G20-G25) % - - - - - <0,3
CO
2
level G31
Max. load
%
9,6 (0 +0,2)
Min. load
9,6 (0 +0,2)
Restricon ΔCO2 max.load - min. load (G31) % CO
2 Min. load ≤ CO2 Max. load
NO
x
level at 80/60 °C max/min
ppm 25/10 30/11 34/16 25/11 22/15 15/15
NO
x
level at 80/60 °C max/min
mg/kWh 44/17 53/19 60/28 44/19 38/27 26/26
NOx emission EN15502 (ppm)
ppm 13,94 18,78 23,61 28,38 22,61 16,84
NOx emission Hi/Hs EN15502 (mg/kWh)
mg/kWh 24,60/22,15 32,61/29,36 40,61/36,57 46,67/42,03 38,19/34,40 29,71/26,76
NOx class EN15502
6
Max. permissible ue resistance
Pa 167 200 200 173 134 200
Water volume l 6 6 6 9 9 9
Water pressure max/min
bar 8/1 8/1 8/1 8/1 8/1 8/1
Max. water temperature
(High limit thermostat)
°C 100 100 100 100 100 100
Maximum temperature setpoint
°C 90 90 90 90 90 90
Nominal water ow at dT=20 K m
3
/h 2,4 2,8 3,2 4,0 4,8 5,6
Hydraulic resistance at nominal ow rate kPa 15 18 22 7 9 11
Electrical connecon
V 230
Frequency
Hz 50
Mains connecon fuse
A 10
IP class with Appliance Type B23(P) - IP30