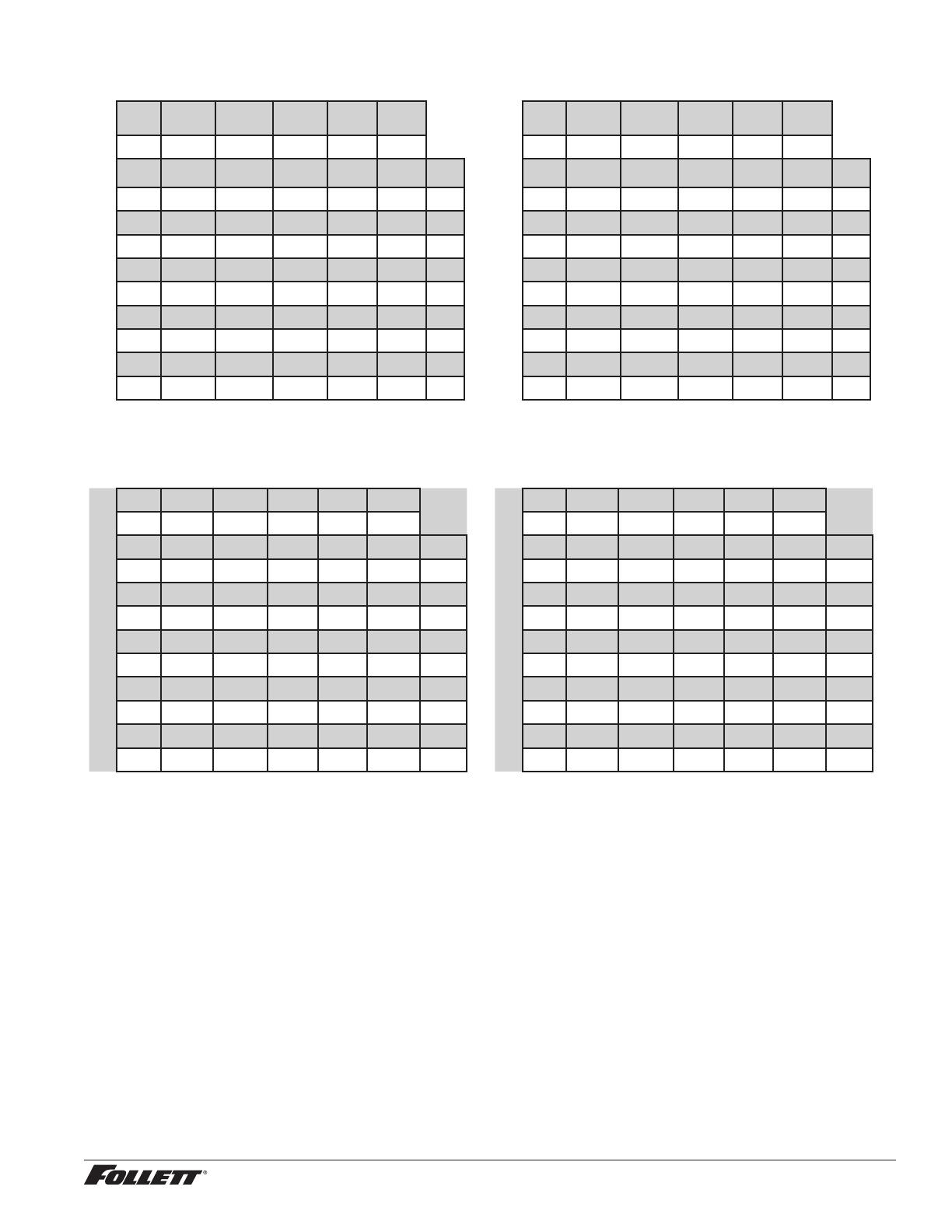
MC_425A/W, MM_425A/W, MF_425A/W, _P425A/W Ice Machines 15
Air-Cooled ice machine capacity/24hrs. - 220 V/60 Hz
Ambient Air Temperature F/C
Inlet Water Temperature F/C
F 60 70 80 90 100
C 16 21 27 32 38
50 454 426 398 363 328 lbs.
10 205 193 181 165 149 kg.
60 437 408 379 346 314 lbs.
16 198 185 172 157 142 kg.
70 420 390 359 330 300 lbs.
21 191 177 163 150 136 kg.
80 401 374 348 319 290 lbs.
27 182 170 158 145 132 kg.
90 381 359 337 308 280 lbs.
32 173 163 153 140 127 kg.
Air-Cooled ice machine capacity/24hrs. - 230 V/50 Hz
Ambient Air Temperature F/C
Inlet Water Temperature F/C
F 60 70 80 90 100
C 16 21 27 32 38
50 460 425 390 355 320 lbs.
10 208 193 177 161 145 kg.
60 437.5 405 372.5 340 307.5 lbs.
16 198 184 169 154 139 kg.
70 415 385 355 325 295 lbs.
21 188 175 161 147 134 kg.
80 405 375 345 315 285 lbs.
27 184 170 156 142 129 kg.
90 395 365 335 305 275 lbs.
32 179 166 152 138 125 kg.
Water-Cooled ice machine capacity/24hrs. -
220 V/60 Hz
Condenser Water Temperature F/C
Inlet Water Temperature F/C
F 60 70 80 90 100
C 16 21 27 32 38
50 454 442 431 419 408 lbs.
10 206 200 195 190 185 kg.
60 435 421 407 394 380 lbs.
16 197 191 185 179 172 kg.
70 416 400 384 368 351 lbs.
21 187 181 174 167 159 kg.
80 396 381 365 350 335 lbs.
27 180 173 166 159 152 kg.
90 375 361 346 332 318 lbs.
32 170 164 157 151 144 kg.
Water-Cooled ice machine capacity/24hrs. -
230 V/50 Hz
Condenser Water Temperature F/C
Inlet Water Temperature F/C
F 60 70 80 90 100
C 16 21 27 32 38
50 429 407 386 364 353 lbs.
10 195 185 175 165 160 kg.
60 409 389 370 350 331 lbs.
16 185 176 168 159 150 kg.
70 389 372 354 336 322 lbs.
21 176 169 161 152 146 kg.
80 370 353 337 320 304 lbs.
27 168 160 153 145 138 kg.
90 349 335 320 315 290 lbs.
32 158 152 145 143 132 kg.
Note: Nominal values - actual production may vary by ±10%.