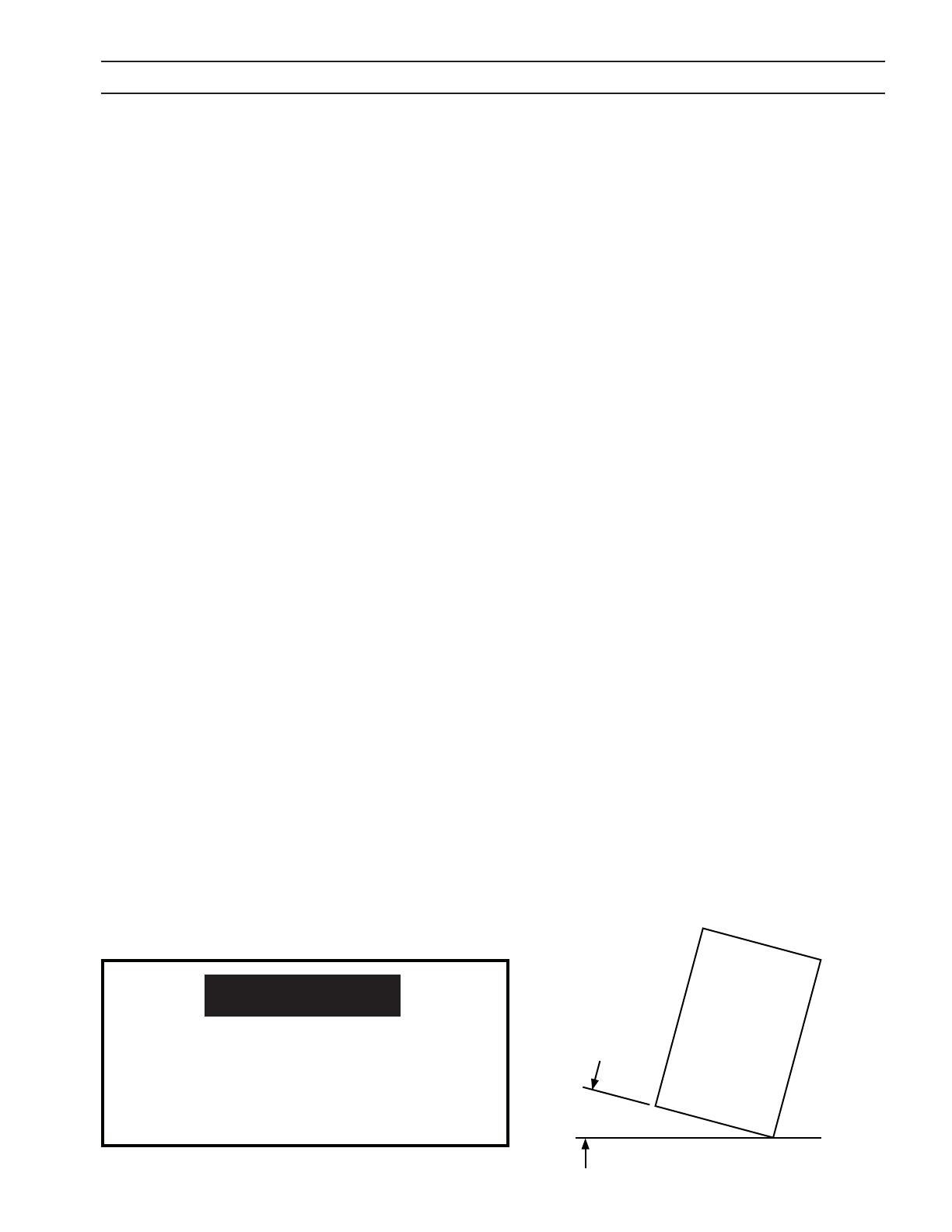
5
SEZIONE 1 INDICAZIONI PER LA SICUREZZA
1.0 Indicazioni per la sicurezza
Gli utenti dell’attrezzatura per la saldatura e il taglio al plasma ESAB hanno la responsabilità di accertarsi che chiunque lavori
al dispositivo o accanto ad esso adotti tutte le idonee misure di sicurezza. Le misure di sicurezza devono soddisfare i requisiti
che si applicano a questo tipo di dispositivo per la saldatura o il taglio al plasma. Attenersi alle seguenti raccomandazioni,
oltre che ai regolamenti standard che si applicano al luogo di lavoro.
Tutto il lavoro deve essere eseguito da personale addestrato, perfettamente al corrente del funzionamento dell’attrezzatura
per la saldatura o il taglio al plasma. Il funzionamento errato dell’attrezzatura può determinare situazioni pericolose con
conseguenti lesioni all’operatore e danni al dispositivo stesso.
1. Chiunque utilizzi attrezzatura per la saldatura o il taglio al plasma deve conoscerne perfettamente:
- il funzionamento
- la posizione degli arresti di emergenza
- la funzione
- le idonee misure di sicurezza
- la saldatura e/o il taglio al plasma
2. L’operatore deve accertarsi che:
- nessuna persona non autorizzata si trovi nell’area operativa dell’attrezzatura quando questa viene messa in
funzione.
- tutti siano protetti quando si esegue l’arco.
3. Il luogo di lavoro deve essere:
- idoneo allo scopo
- privo di correnti d’aria
4. Attrezzature per la sicurezza personale:
- indossare sempre l’attrezzatura di sicurezza personale raccomandata, come occhiali di sicurezza,
abbigliamento ignifugo, guanti di sicurezza.
- non indossare oggetti sporgenti, come sciarpe, braccialetti, anelli, ecc., che potrebbero rimanere
intrappolati o causare ustioni.
5. Precauzioni generali:
- accertarsi che il cavo di ritorno sia collegato saldamente;
- il lavoro su apparecchiature ad alta tensione può essere eettuato sono da parte di tecnici qualicati;
- i dispositivi antincendio idonei devono essere indicati chiaramente e a portata di mano;
- durante il funzionamento non eettuare lavori di lubricazione e manutenzione.
Il codice IP indica la classe del contenitore, cioè il livello di protezione contro la penetrazione di oggetti solidi o acqua. La
protezione viene fornita per evitare l’inserimento di dita, la penetrazione di oggetti solidi più grandi di 12 mm e gli spruzzi
di acqua no a 60 gradi di inclinazione rispetto alla verticale. Le attrezzature marcate IP21S possono essere immagazzinate,
ma non devono essere usate all’aperto in presenza di precipitazione senza un adeguato riparo.
Classe del contenitore
15°
Inclinazione
massima
consentita
ATTENZIONE
Se l’apparecchiatura è collocata su una
superficie inclinata più di 15° si potrebbe
vericare un ribaltamento, con conseguenti
rischi di lesioni personali e/o danni rilevanti
all’attrezzatura.