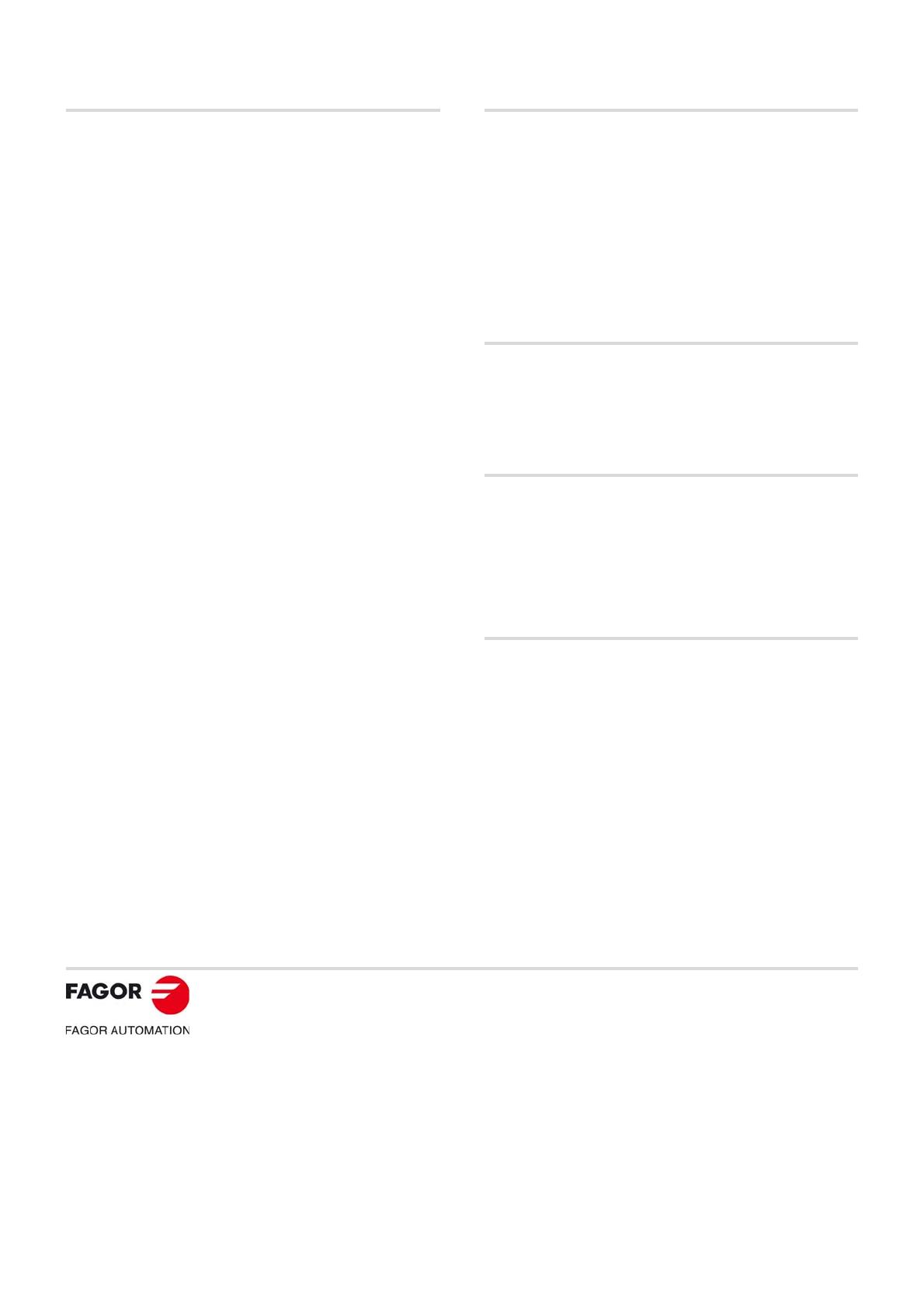
PAGINA IN BIANCO
·2·
Tutti i diritti sono riservati. La presente documentazione, interamente o in parte,
non può essere riprodotta, trasmessa, trascritta, memorizzata in un sistema di
registrazione dati o tradotta in nessuna lingua, senza autorizzazione espressa
di Fagor Automation. È vietata la copia, parziale o totale, o uso non autorizzato
del software.
L'informazione di cui al presente manuale può essere soggetta a variazioni
dovute a eventuali modifiche tecniche. La Fagor Automation si riserva il diritto
di modificare il contenuto del manuale senza preavviso.
Tutti i marchi registrati o commerciali riportati nel manuale appartengono ai
rispettivi proprietari. L’uso di tali marchi da parte di terzi a fini privati può vulnerare
i diritti dei proprietari degli stessi.
È possibile che il CNC possa eseguire più funzioni di quelle riportate nella relativa
documentazione; tuttavia Fagor Automation non garantisce la validità di tali
applicazioni. Pertanto, salvo dietro espressa autorizzazione della Fagor
Automation, qualsiasi applicazione del CNC non riportata nella documentazione,
deve essere considerata "impossibile". FAGOR AUTOMATION non si rende
responsabile degli infortuni alle persone, o dei danni fisici o materiali di cui possa
essere oggetto o provocare il CNC, se esso si utilizza in modo diverso a quello
spiegato nella documentazione connessa.
È stato verificato il contenuto del presente manuale e la sua validità per il prodotto
descritto. Ciononostante, è possibile che sia stato commesso un errore
involontario e perciò non si garantisce una coincidenza assoluta. In ogni caso,
si verifica regolarmente l’informazione contenuta nel documento e si provvede
a eseguire le correzioni necessarie che saranno incluse in una successiva
editazione. Si ringrazia per i suggerimenti di miglioramento.
Gli esempi descritti nel presente manuale sono orientati all’apprendimento.
Prima di utilizzarli in applicazioni industriali, devono essere appositamente
adattati e si deve inoltre assicurare l’osservanza delle norme di sicurezza.
SICUREZZA DELLA MACCHINA
È responsabilità del costruttore della macchina che le sicurezze della stessa
siano abilitate, allo scopo di evitare infortuni alle persone e prevenire danni al
CNC o agli elementi collegati allo stesso. Durante l'avvio e la conferma dei
parametri del CNC, si verifica lo stato delle seguenti sicurezze. Se uno di essi
è disabilitato, il CNC riporta un messaggio di avviso.
• Allarme di retroazione per assi analogici.
• Limiti di software per assi lineari analogici e sercos.
• Monitoraggio dell'errore di inseguimento per assi analogici e sercos (eccetto
il mandrino), sia sul CNC che sui regolatori.
• Test di tendenza sugli assi analogici.
FAGOR AUTOMATION non si rende responsabile degli infortuni alle persone,
o dei danni fisici o materiali di cui possa essere oggetto o provocare il CNC,
imputabili all'annullamento di alcune delle sicurezze.
PRODOTTI DOPPIO USO.
I prodotti fabbricati dalla FAGOR AUTOMATION a partire dal 1ºaprile 2014, se
contenuti nell’elenco dei prodotti a doppio uso, secondo il regolamento UE
428/2009, comprendono nell’identificazione prodotto la scritta -MDU e
necessitano di licenza export in base alla destinazione.
TRADUZIONE DEL MANUALE ORIGINALE
Il presente manuale è una traduzione del manuale originale. Il presente manuale,
come i documenti ad esso correlati, sono stati redatti in lingua spagnola. In caso
di contraddizioni tra il documento in lingua spagnola e le sue traduzioni, prevarrà
la redazione in lingua spagnola. Il manuale originale sarà identificato dal testo
"MANUALE ORIGINALE".
AMPLIANTI DI HARDWARE
FAGOR AUTOMATION non si rende responsabile degli infortuni alle persone,
o dei danni fisici o materiali di cui possa essere oggetto o provocare il CNC,
imputabili a una modifica dell'hardware da parte di personale non autorizzato
dalla Fagor Automation.
La modifica dell'hardware del CNC da parte di personale non autorizzato dalla
Fagor Automation implica la perdita della garanzia.
VIRUS INFORMATICI
FAGOR AUTOMATION garantisce che il software installato non contiene nessun
virus informatico. È responsabilità dell'utente mantenere l'apparecchiatura
esente da virus, allo scopo di garantirne il corretto funzionamento. La presenza
di virus informatici sul CNC può provocarne il cattivo funzionamento.
FAGOR AUTOMATION non si rende responsabile degli infortuni alle persone,
o dei danni fisici o materiali di cui possa essere oggetto o provocare il CNC,
imputabili alla presenza di virus informatici nel sistema.
La presenza di virus informatici nel sistema implica la perdita della garanzia.