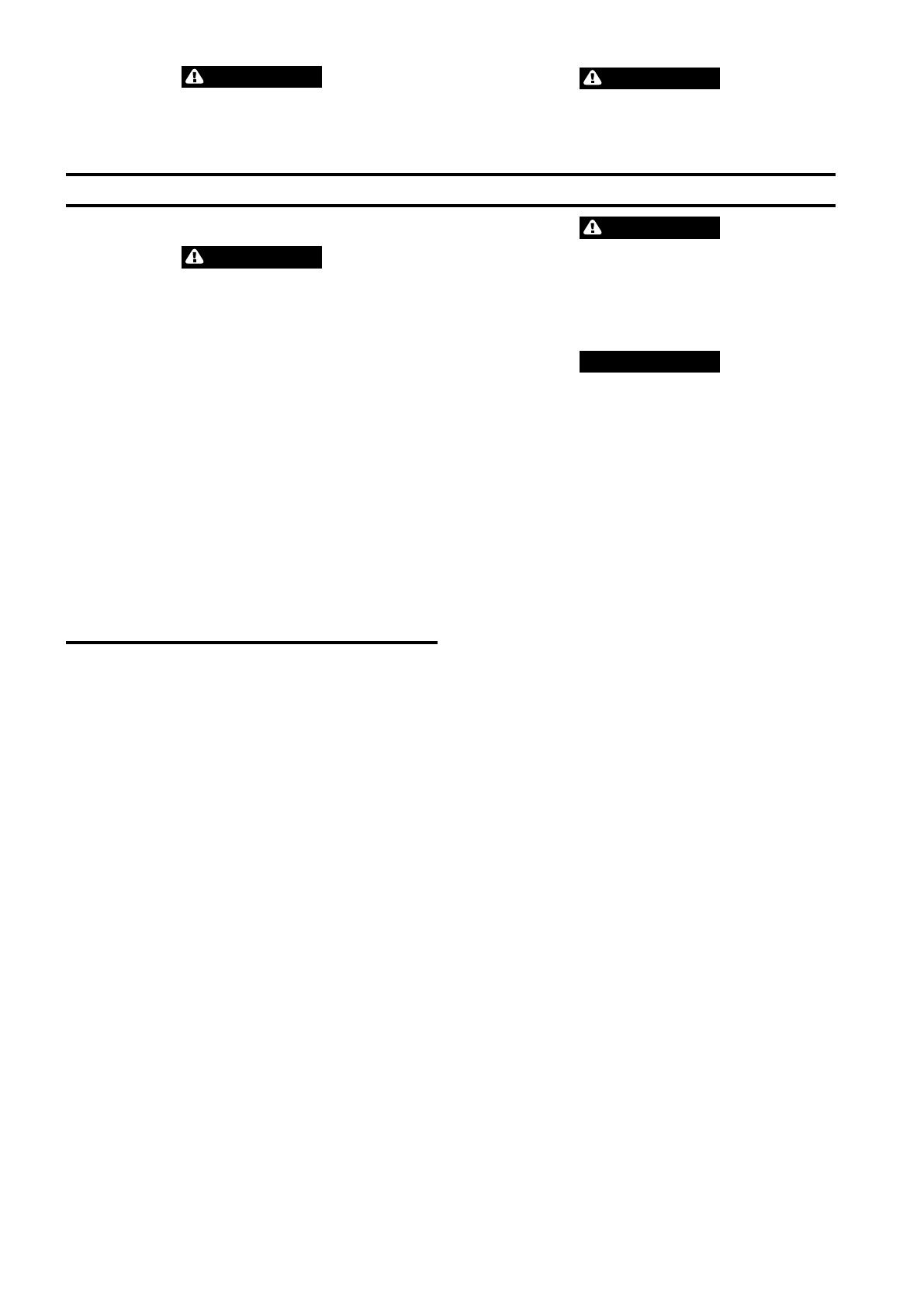
WARNING
• The line used to pull down the Man Riding device must be attached in such
a manner as to NOT pull on the suspended person or tip the Man Riding device.
2. Alternatively, send additional weight to the suspended person using another line.
This weight must be secure and evenly distributed. Never exceed the capacity of
the winch or man riding device.
CAUTION
• Any additional weight should be sent in small, easily handled bundles and
only enough to cause person to lower. When lowering person in this manner
the brake(s) can be used to control lowering by releasing air pressure or
applying the band brake.
INSPECTION
Inspection information is based in part on American Society of Mechanical Engineers
Safety Codes B30.7.
WARNING
• All new or repaired equipment should be inspected and tested by
Ingersoll Rand trained Service Technicians to ensure safe operation at rated
specifications before placing equipment in service.
• Never use a winch that inspection indicates is damaged.
Frequent and quarterly inspections should be performed on equipment in regular
service. Frequent inspections are visual examinations performed by operators or
Ingersoll Rand trained Inspectors and include observations made during routine
equipment operation. Quarterly inspections are thorough inspections conducted by
Ingersoll Rand trained Service Technicians. ASME B30.7 states inspection intervals
depend upon the nature of the critical components of the equipment and the severity
of usage. Refer to ‘Inspection Classifications’ chart and ‘Maintenance Intervals’ chart
in Product Maintenance Information Manual for recommended maintenance intervals.
Careful inspection on a regular basis will reveal potentially dangerous conditions
while still in the early stages, allowing corrective action to be taken before the
condition becomes dangerous.
Deficiencies revealed through inspection, or noted during operation, must be reported
to designated personnel to ensure corrective action is taken.
A determination as to whether a condition constitutes a safety hazard(s) must be
decided, and the correction of noted safety hazard(s) accomplished and documented
by written report before placing the equipment in service.
n Wire Rope Reports
Records should be maintained as part of a long-range wire rope inspection program.
Records should include the condition of wire rope removed from service. Accurate
records will establish a relationship between visual observations noted during
frequent inspections and the actual condition of wire rope as determined by quarterly
inspections.
n
Frequent Inspection
On equipment in continuous service, a ‘Daily Inspection’ should be made by the
operator at the beginning of each shift and a ‘Quarterly Inspection’ should be
conducted by an Ingersoll Rand trained Inspector every 90 days and a record of the
inspection maintained.
n Daily Inspection
Complete inspections prior to start of daily tasks. Conduct visual inspections during
regular operation for indications of damage or evidence of malfunction (such as
abnormal noises).
1.
Lubricator: Adjust air line lubricator drops [ISO VG 46 (SAE 10W)] per minute to
6 to 9 during winch operation.
2.
Motor Oil Level: Check motor oil level. Drain condensate and top off oil level.
3.
Surrounding Area: Visually check for winch oil leaks. Do not operate winch if
leaking oil is found. Ensure surrounding area has no slippery surfaces and is
obstruction free.
4.
Hoses and Fittings: Visually inspect for damage, air leaks, and loose connections.
Repair all leaks or damage and tighten loose connections prior to starting daily
tasks.
5.
Muffler: Visually check for restrictions or external damage. Clear restrictions or
replace if damaged.
6.
Wire Rope Anchor: Verify wire rope anchor is securely installed.
7.
Guards: Verify wire rope does not contact drum guard during winch operation and
that guards are secure and undamaged.
8.
Winch: Visually inspect winch housings, control(s), external brake, siderails,
uprights and drum for damage. Check that all external bolts are in place and
secure. Report damage to supervisor and request additional inspection by an
Ingersoll Rand trained service technician.
9.
Mounting: Visually inspect winch mounting bolts. Check bolts are tight,
undamaged and free of corrosion.
10.
Winch Operation: Power winch in both directions. Winch must operate smoothly
without sticking, binding or abnormal noises and have minimal vibration.
11.
Control Valve: Check operation is smooth and winch is responsive to control
device movement. Lever must return to neutral and lock in place when released.
If winch responds slowly or control sticks, do not operate until problems are
corrected. Winch is to operate without hesitation in either payout and haul-in
direction.
12.
Wire Rope Spooling: Visually check reeving and ensure wire rope feeds on and
off the drum smoothly. Verify spooling direction is correct for winch and
application.
13.
Brakes: Lift and lower the load a short distance to test brakes. Brakes must hold
load without slipping. Automatic brake must release when winch control throttle
is operated. If brakes do not hold load or do not release properly, they must be
adjusted or repaired.
WARNING
• Worn or improperly functioning brakes may cause excessive heat buildup and
sparks.
14.
Wire Rope: Visually inspect all wire rope expected to be in use during the day’s
operations. Inspect for wear and damage indicated by distortion of wire rope such
as kinking, “birdcaging,” core protrusion, main strand displacement, corrosion,
broken or cut strands. If damage is evident, do not operate winch until the
discrepancies have been reviewed and inspected further by personnel
knowledgeable on wire rope safety and maintenance procedures.
NOTICE
• The full extent of wire rope wear cannot be determined by visual inspection.
At any indication of wear inspect wire rope in accordance with instructions
in “Quarterly Inspection”. Refer to Product Maintenance Information Manual.
15.
Limit Switches: Ensure limit switches engage and prevent operation at the
required set point and with drum rotating in the correct direction. Ensure limit
switch properly resets.
16.
Emergency Stop Valve: Activate emergency stop in payout and haul-in directions
to ensure proper operation. Valve must stop winch operation and brake must set
quickly. Reset valve after test.
17.
Slack Line Detection: Operate winch in payout direction until slack line valve
actuates. Ensure winch stops running in lowering direction, but can still lift load.
18.
Press Roller: Ensure wire rope is positioned between press roller and drum barrel
and springs keep press roller in tight contact with wire rope. Ensure smooth and
proper operation.
19.
Motor: During operation check motor housing for excess heat build up. Housing
should not be hot to touch. Listen for grinding or knocking noises. If excess heat
or noises are noted, do not operate until inspected by an Ingersoll Rand trained
service technician.
n Quarterly Inspection
Complete a ‘Quarterly Inspection’ on a recurring basis to provide regular winch
monitoring.
In addition to the requirements of ‘Daily Inspection’ also inspect the following:
1.
Power Supply:
- Inlet air pressure to the winch is 90 psi (6.3 bar) at full throttle with nominal
system usage
- Filter, regulator and lubricator are installed and functioning
- Air filter is clean, drain if necessary
- Air supply regulator is set to 90 psi (6.3 bar)
2.
Rigging:
- Correct size wire rope is being used. 10 mm minimum
- Wire rope take-off angle is within design limits
3.
Visual Integrity:
- All Components - Inspect for wear, damage, distortion, deformation and
cleanliness. If external evidence indicates damage, contact Ingersoll Rand
Service Technician to disassemble as required to conduct a detailed
inspection
- No part of the winch has been welded onto
- Fasteners - Check external retainer rings, split pins, capscrews, nuts and other
fasteners on winch, including mounting bolts
- Drum and Sheaves - Check for cracks, wear or damage
- Press Roller - Inspect rollers for wear and grooves. Ensure rollers freely rotate.
Replace rollers if worn or grooved. Replace bearings if rotation is rough or
stiff
- Slack Line Detector - Inspect rollers for wear and grooves. Ensure rollers freely
rotate
- Ensure drum guard is capable of adequately guarding personnel
- No modifications have been performed on the winch
- Check motor, gearbox and disc brake for oil leakage
4.
Labeling / Marking:
- Data (name) plate is attached and legible
- Warning tags and labels are attached, legible and in correct places on winch
5.
Wire Rope Spooling:
- A minimum of 3 dead wraps remain on drum in fully paid-out position
- Proper freeboard is maintained at full haul-in position (minimum 1 inch (26
mm) for 10 mm wire rope)
- Wire rope is properly lubricated
6.
Operational Checks:
- Automatic Band Brake and Disc Brake: Ensure that both brakes hold the load.
- Limit Switches - Operate winch in the haul-in direction until limit switch
engages. Ensure winch stops running in haul-in direction, and operate in
payout. Operate winch in payout direction until limit switch engages. Ensure
winch stops operating in payout direction, and will operate in haul-in
direction
- Line Speed - Raise and lower (5 ft. min. distance) a 485 lbs (220 kg) load at
first layer to verify line speed. Line speed to be 60 fpm (18 m/min). Line
speed to be recorded after warm-up
8
Form MHD56470 Edition 4