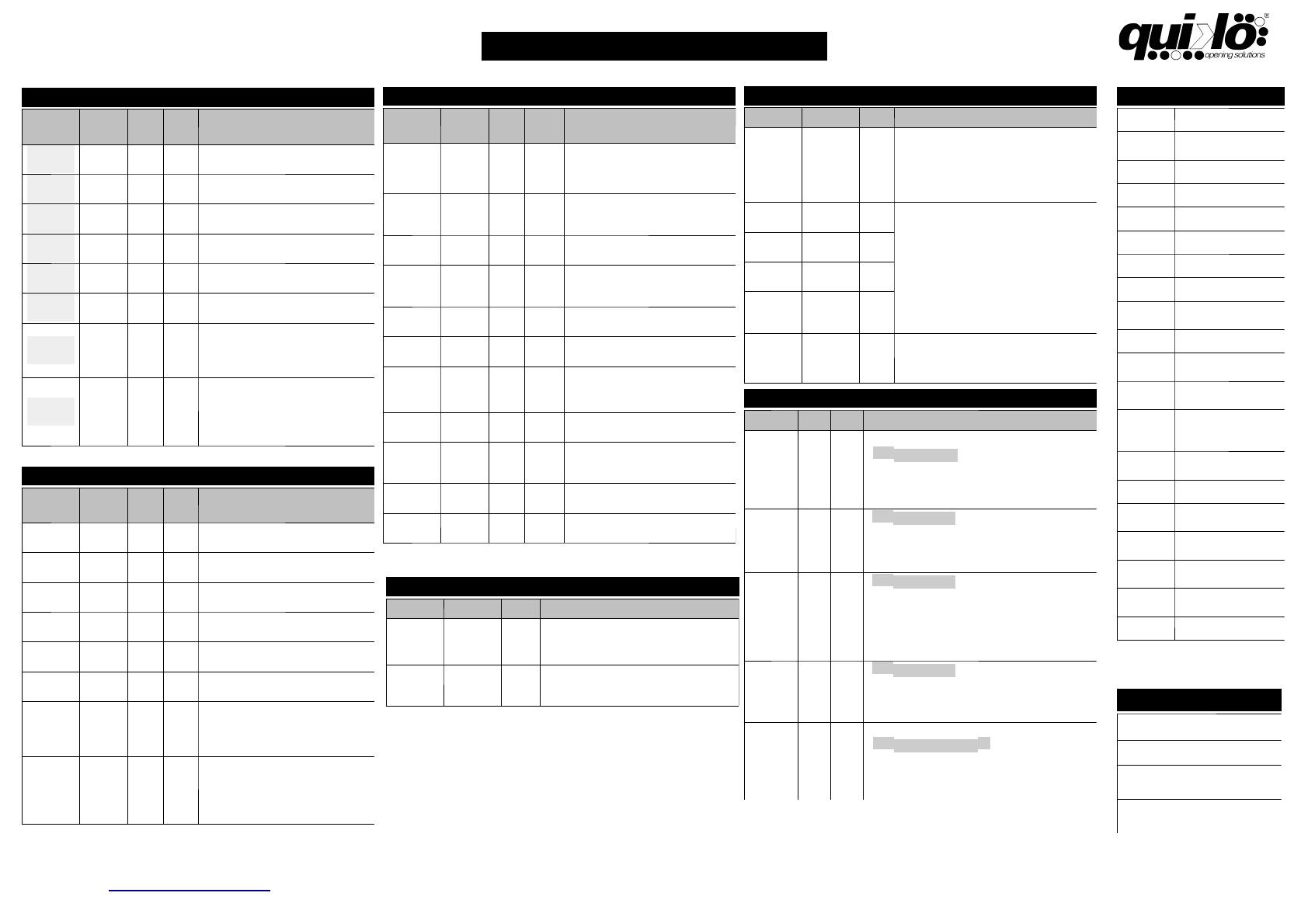
SOMMARIO
Impostazioni motore B
DISPLAY DEFAULT @ C
MAX
@ D
MIN DESCRIZIONE
B1 14
sec
99
sec
00
sec Tempo di lavoro normale.
b2 7
sec
99
sec
00
sec Tempo di lavoro in rallentamento
b3 0.8
sec
1.5
sec
0.1
sec Tempo di avvio.
b4 3
sec
99
sec
0
sec Sfasamento in apertura.
b5 6 10 1 Forza normale.
b6 8 10 1 Forza rallentamento.
b7 NO 99 - NO 0
Soglia sensore di sforzo modalità
normale. Durante la chiusura, per il
tempo di lavoro normale, i display
mostrano lo sforzo del motore B.
b8 NO 99 - NO 0
Soglia sensore di sforzo modalità
rallentamento. Durante la chiusura,
per il tempo di lavoro in
rallentamento i display mostrano lo
sforzo del motore B.
Funzioni di cortesia
DISPLAY DISPLAY @ CDESCRIZIONE
d0 no Imposta
Per ripristinare il default mantenere
premuto il tasto @ C finché I display non
mostrano --
P2 __ X
Quando un commando di start è ricevuto
la centrale avvia una procedura di
acquisizione dei tempi di manovra.
Segnalazioni
St Stop.
FH Fotocellule esterna ed
interna.
tA Fotocellula interna.
tC Fotocellula esterna
td Fotocellula esterna
Go Start.
oP Apri.
CL Chiudi.
Eo Comando QK-
SMARTM.
PE Start pedonale.
A* Fine corsa motore A
apertura o chiusura.
*B Fine corsa motore B
apertura o chiusura.
Ab Fine corsa motore A e
motore B apertura o
chiusura.
- Telecomando in
trasmissione
1t Errore test fotocellule.
7A Rilevazione ostacolo
motore A.
9A Motore A in protezione
termica.
7b Rilevazione ostacolo
motore B.
9b Motore B in protezione
termica.
FF Memoria radio piena.
Funzioni
DISPLAY DEFAULT @ C
MAX
@ D
MIN DESCRIZIONE
F0 10
sec
99
sec
00
sec
Tempo di pausa. Per disabilitare
tenere premuto il tasto @ C finché il
display non mostra 5t.
F2 0
sec
0.5
sec
0.0
sec
Colpo di chiusura. Può essere
utile quando viene installata l'elettro-
serratura.
F3 0.0
sec
4.0
sec
00
sec Tempo di prelampeggio.
F4 NO SI NO
Colpo d'ariete. Può essere utile
quando viene installata l'elettro-
serratura.
F5 NO SI SI Passo passo.
F6 NO SI NO Condominiale.
F8 SI SI NO
Logica fotocellule.
SI = Logica Battente
no = Logica Scorrevole.
L0 NO SI NO Modulo Elettro-serratura.
L1 00 00
min
10
min
Funzione inverno freddo. Questa
funzione è utile in paesi dove
l'inverno è estremamente freddo.
t1 NO SI NO Test fotocellule.
t2 SI SI NO Test motori in termico.
Impostazioni motore A
DISPLAY DEFAULT @ C
MAX
@ D
MIN DESCRIPTION
A1 14
sec
99
sec
00
sec Tempo di lavoro normale.
A2 7
sec
99
sec
00
sec Tempo di lavoro in rallentamento.
A3 0.8
sec
1.5
sec
0.1
sec Tempo di avvio.
A4 6
sec
99
sec
0
sec Sfasamento in chiusura.
A5 6 10 1 Forza normale.
A6 8 10 1 Forza rallentamento.
A7 NO 99 - NO 0
Soglia sensore di sforzo modalità
normale. Durante l'apertura, per il
tempo di lavoro normale, I display
mostrano lo sforzo del motore A.
A8 NO 99 - NO 0
Soglia sensore di sforzo modalità
rallentamento. Durante l'apertura, per
il tempo di lavoro in rallentamento i
display mostrano lo sforzo del motore
A.
www.quikoitaly.com 2 di 12
TASTI
@ A Scorre il menù in avanti.
@ B Scorre il menù all'indietro.
@ C Incrementa o imposta SI
SI significa: Abilitato/a.
@ D Decrementa o imposta no
no significa: Disabilitato/a.
Funzioni radio
DISPLAY DISPLAY @ CDESCRIZIONE
r0 1...2... Elimina
Cancella il codice mostrato:
Quando il display mostra il codice
identificativo del telecomando da cancellare
mantenere premuto il tasto @ C finché il
display non si spegne: **.
r1 =_ Salva Per salvare un telecomando: Mantenere
premuto il tasto del telecomando. I display
mostrano _, premere il tasto @ C della
centrale.
r1 →Start
r2 →Stop
r3 →Start Pedonale
r4 →Chiusura rapida
r2 =_ Salva
r3 =_ Salva
r4 =_ Salva
r5 no Elimina
Elimina tutti I codici:
Mantenere premuto il tasto @ C finché I
display non mostrano SI fisso.
Impostazioni ingressi
DISPLAY @ C@ DDESCRIZIONE
E1 ↓ ↑
no = Disabitato.
Go = Start (N.A.)
oP = Apri (N.A.).
CL = Chiudi (N.A.).
Eo = comando QK-SMARTM (N.A.)
E2 ↓ ↑
no = Disabitato.
St = Stop (N.C.)
A* = Fine corsa motore A apertura
e chiusura ( N.A.).
E3 ↓ ↑
no = Disabitato.
tC = Fotocellula Esterna (N.C.)
td = Come tC ma con la
possibilità di aprire il cancello anche
quando la fotocellula esterna sta rilevando
un ostacolo.
E4 ↓ ↑
no = Disabitato.
tA = Fotocellula interna (N.C.)
*B = Fine corsa motore B apertura
e chiusura ( N.A.).
E7 ↓ ↑
no = Disabitato.
PE = Pedonale (N.A.)
oP = Apri ( N.A. ).
CL = Chiudi ( N.A. ).
Eo = comando QK-SMARTM (N.A.)