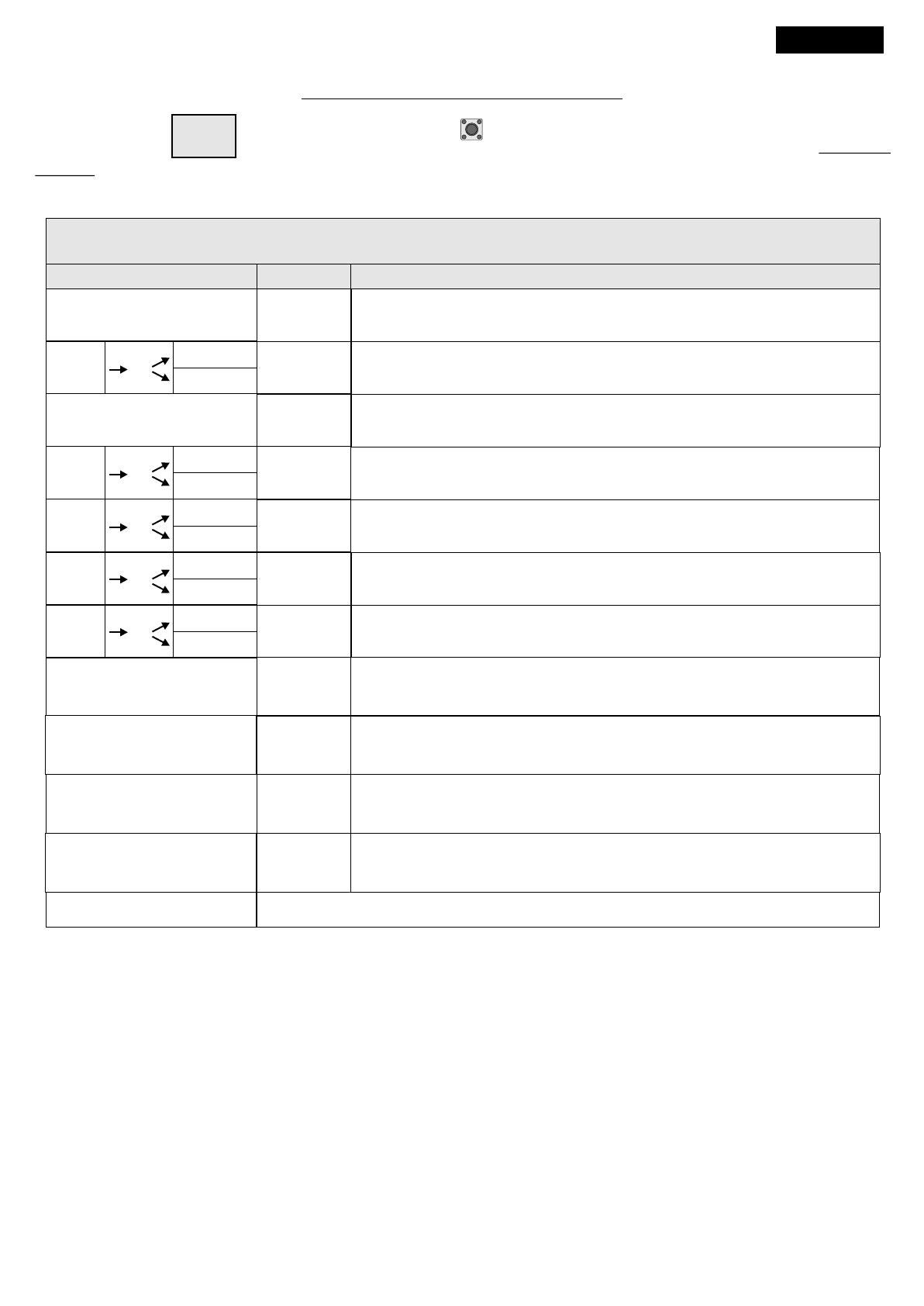
MENU
Description
Description
Start test
Stop test
Partial opening
start test
Safety edge1
test
Photocell 1
test
Photocell 2
test
M1 Opening
limit switch
test
M1 Closing
limit switch
test
The contact must be a N.O. Contact . When activating the related command
on the display SET lights up, the input works.
If SET is always on, check the wirings.
The contact must be a N.C. Contact. When activating the related command
on the display SET lights up, the input works.
If SET is always on, make sure that the contact is a N.C. Contact
The contact must be a N.C. Contact. When activating the related command
on the display SET lights up, the input works. If SET is always on, make
sure that the contact is a N.C. contact or that the related limit switch is not occupied.
The contact must be a N.O. Contact. When activating the related command
on the display SET lights up, the input works.
If SET is always on, check the wirings.
The contact must be a N.C. Contact. When activating the related command
on the display SET lights up, the input works.
If SET is always on, make sure that the contact is a N.C. Contact
IThe contact must be a N.C. Contact. When activating the related command
on the display SET lights up, the input works.
If SET is always on, make sure that the contact is a N.C. Contact
The contact must be a N.C. Contact. When activating the related command
on the display SET lights up, the input works.
If SET is always on, make sure that the contact is a N.C. Contact
The contact must be a N.C. Contact. When activating the related command
on the display SET lights up, the input works. If SET is always on, make
sure that the contact is a N.C. Contact or that the related limit switch is not occupied.
Exit menu
OK
OK
OK
MENU FUNCTION TABLE CHECK GATE 2 DG R1B INPUTS
To access the Menu for input check keep pressed OK for about 5 seconds.
OK
Safety edge2
test
The contact must be a N.C. Contact. When activating the related command
on the display SET lights up, the input works.
If SET is always on, make sure that the contact is a N.C. Contact
OK
M2 Opening
limit switch
test
M2 Closing
limit switch
test
The contact must be a N.C. Contact. When activating the related command
on the display SET lights up, the input works. If SET is always on, make
sure that the contact is a N.C. contact or that the related limit switch is not occupied.
The contact must be a N.C. Contact. When activating the related command
on the display SET lights up, the input works. If SET is always on, make
sure that the contact is a N.C. Contact or that the related limit switch is not occupied.
Note: If the Stop, Photocell 1 and Photocell 2, Edge 1 and Enge 2 contacts are not bridged in self-learning, they will be deactivated and
can be reactivated through this menu, without repeating times self-learning.
LIMIT SWITCH
CLOSING 1
LIMIT SWITCH
OPENING 1
START
EDGE1
PHOTO1
PHOTO2
PARTIAL OPENING START
END
STOP
Enabled
Blocked
LIMIT SWITCH
CLOSING 2
LIMIT SWITCH
OPENING 2
Enabled
Blocked
Enabled
Blocked
Enabled
Blocked
EDGE2
Enabled
Blocked
Moving in the menu pressing the button for 5 seconds, you enter the CHECK
MENU, where you can check the operating status of all inputs.
INPUTS CHECK MENU
MENU
SEA
SET
1-LANGUAGE
OK
40
English